申請日2015.09.01
公開(公告)日2015.12.23
IPC分類號C02F1/40; C02F1/56; C02F1/52; C02F1/24
摘要
本發(fā)明提供一種含油污水處理裝置,包括:除油凈化裝置,用于將含油污水進行油水分離,得到含油浮渣和清水;及與除油凈化裝置連通的浮渣分離裝置,用于將含油浮渣經(jīng)脫水處理后進行油水分離,得到浮渣、污油和水。本發(fā)明還提供一種含油污水處理方法。上述處理裝置及處理方法,采用除油凈化裝置和浮渣分離裝置,先將含油污水進行油水分離,得到含油浮渣和清水,再將含油浮渣經(jīng)脫水處理后進行油水分離,得到浮渣、污油和水。含油污水中污油去除率可達96%以上,浮渣減量率在70%以上。
摘要附圖
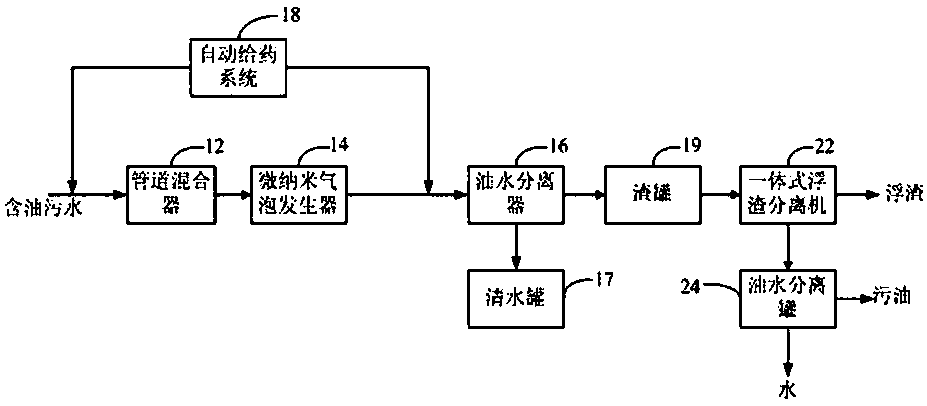
權(quán)利要求書
1.一種含油污水處理裝置,其特征在于,包括:
除油凈化裝置,用于將含油污水進行油水分離,得到含油浮渣和清水;及
與所述除油凈化裝置連通的浮渣分離裝置,用于將所述含油浮渣經(jīng)脫水處理后進行油水分離,得到浮渣、污油和水。
2.根據(jù)權(quán)利要求1所述的含油污水處理裝置,其特征在于,所述除油凈化裝置包括:
管道混合器,用于將含油污水與除油分散劑混合,得到混合液;
與所述管道混合器連通的微納米氣泡發(fā)生器,用于使所述混合液中產(chǎn)生大量的微納米氣泡,形成氣水混合物;及
與所述微納米氣泡發(fā)生器連通的油水分離器,用于將所述氣水混合物與高效助劑混合后進行油水分離,得到含油浮渣和清水。
3.根據(jù)權(quán)利要求2所述的含油污水處理裝置,其特征在于,所述除油凈化裝置還包括自動給藥系統(tǒng),所述自動給藥系統(tǒng)用于分別投加所述除油分散劑和所述高效助劑。
4.根據(jù)權(quán)利要求2所述的含油污水處理裝置,其特征在于,所述浮渣分離裝置包括:
與所述油水分離器連通的一體式浮渣分離機,用于將所述含油浮渣進行脫水處理,得到浮渣和油水混合液;及
與所述一體式浮渣分離機連通的油水分離罐,用于將所述油水混合液進行油水分離,得到污油和水。
5.根據(jù)權(quán)利要求4所述的含油污水處理系統(tǒng),其特征在于,所述含油污水處理裝置還包括清水罐和渣罐,所述清水罐與所述油水分離器連通,所述油水分離器通過所述渣罐與所述一體式浮渣分離機連通。
6.一種含油污水處理方法,其特征在于,包括以下步驟:
將含油污水進行油水分離,得到含油浮渣和清水;及
將所述含油浮渣經(jīng)脫水處理后進行油水分離,得到浮渣、污油和水。
7.根據(jù)權(quán)利要求6所述的含油污水處理方法,其特征在于,所述將含油污水進行油水分離,得到含油浮渣和清水的步驟具體為:
將含油污水與除油分散劑混合,得到混合液;
使所述混合液中產(chǎn)生大量的微納米氣泡,形成氣水混合物;及
將所述氣水混合物與高效助劑混合后進行油水分離,得到含油浮渣和清水。
8.根據(jù)權(quán)利要求7所述的含油污水處理方法,其特征在于,所述除油分散劑為聚合氯化鋁鐵、聚合氯化鋁、聚合氯化鐵或聚合硫酸鐵;所述除油分散劑的濃度為50mg/L~2000mg/L;所述高效助劑為聚丙烯酰胺;所述聚丙烯酰胺的濃度為6mg/L~200mg/L。
9.根據(jù)權(quán)利要求7所述的含油污水處理方法,其特征在于,將所述含油浮渣經(jīng)脫水處理后進行油水分離,得到浮渣、污油和水的步驟具體為:
將所述含油浮渣進行脫水處理,得到浮渣和油水混合液;及
將所述油水混合液進行油水分離,得到污油和水。
10.根據(jù)權(quán)利要求6所述的含有污水處理方法,其特征在于,在所述將含油污水進行油水分離的步驟之前還包括以下步驟:
將所述含油污水進行過濾。
說明書
含油污水處理裝置及處理方法
技術(shù)領(lǐng)域
本發(fā)明涉及化工領(lǐng)域,特別是涉及一種含油污水處理裝置及處理方法。
背景技術(shù)
延遲焦化工藝是目前重質(zhì)油高效加工的主要方法之一。延遲焦化工藝的主要加工原料為:減底渣油、催化油漿、罐區(qū)冷渣、瀝青渣等,這些原料在加工過程中會產(chǎn)生大量的含油污水,該含油污水中主要包括“冷焦”過程中產(chǎn)生的大吹氣冷凝水、冷焦水、切焦水等。該部分含油污水不僅含大量乳化嚴重的輕質(zhì)污油組分、酚類、多環(huán)芳香族及含氮、氧、硫的雜環(huán)化合物等,而且富含多種極易揮發(fā)的惡臭氣體。
由于國內(nèi)對該含油污水的處理技術(shù)還不太成熟,絕大部分煉廠對該部分含油污水一般都采取簡單的沉降脫水,然后用大量水稀釋后,直排進下游的污水處理系統(tǒng)的處理方式。高油含量組分對污水處理廠的負荷沖擊非常大,尤其影響后續(xù)的生化處理,直接影響總排出水的油含量、COD等控制指標(biāo)。因此,如何高效處理延遲焦化裝置含油污水成為困擾各大煉廠的一個難題,受到越來越多煉廠的重視。
含油浮渣具有產(chǎn)生量大、含水率高、重質(zhì)油組分高、綜合利用方式少、脫水處理難度大等特點。由于其存在對周圍的環(huán)境質(zhì)量有著不良影響,國內(nèi)多數(shù)煉廠一般采用離心脫水工藝處理,但結(jié)果都不甚理想,主要表現(xiàn)在:浮渣中油水難分離,含油浮渣的含水率多在75%~85%之間,過濾后水中懸浮物含量高、處理成本大且離心過濾設(shè)備因長期高速旋轉(zhuǎn)、能耗高等。
綜上所述,尋找一種能高效去除含油污水中的污油、浮渣的含油污水處理裝置及處理方法成為當(dāng)務(wù)之急。
發(fā)明內(nèi)容
基于此,提供一種能高效去除含油污水中的污油、浮渣的含油污水處理裝置。
此外,還提供一種含油污水處理方法。
一種含油污水處理裝置,包括:
除油凈化裝置,用于將含油污水進行油水分離,得到含油浮渣和清水;及
與所述除油凈化裝置連通的浮渣分離裝置,用于將所述含油浮渣經(jīng)脫水處理后進行油水分離,得到浮渣、污油和水。
在其中一個實施例中,所述除油凈化裝置包括:
管道混合器,用于將含油污水與除油分散劑混合,得到混合液;
與所述管道混合器連通的微納米氣泡發(fā)生器,用于使所述混合液中產(chǎn)生大量的微納米氣泡,形成氣水混合物;及
與所述微納米氣泡發(fā)生器連通的油水分離器,用于將所述氣水混合物與高效助劑混合后進行油水分離,得到含油浮渣和清水。
在其中一個實施例中,所述除油凈化裝置還包括自動給藥系統(tǒng),所述自動給藥系統(tǒng)用于分別投加所述除油分散劑和所述高效助劑。
在其中一個實施例中,所述浮渣分離裝置包括:
與所述油水分離器連通的一體式浮渣分離機,用于將所述含油浮渣進行脫水處理,得到浮渣和油水混合液;及
與所述一體式浮渣分離機連通的油水分離罐,用于將所述油水混合液進行油水分離,得到污油和水。
在其中一個實施例中,所述含油污水處理裝置還包括清水罐和渣罐,所述清水罐與所述油水分離器連通,所述油水分離器通過所述渣罐與所述一體式浮渣分離機連通。
一種含油污水處理方法,包括以下步驟:
將含油污水進行油水分離,得到含油浮渣和清水;及
將所述含油浮渣經(jīng)脫水處理后進行油水分離,得到浮渣、污油和水。
在其中一個實施例中,所述將含油污水進行油水分離,得到含油浮渣和清水的步驟具體為:
將含油污水與除油分散劑混合,得到混合液;
使所述混合液中產(chǎn)生大量的微納米氣泡,形成氣水混合物;及
將所述氣水混合物與高效助劑混合后進行油水分離,得到含油浮渣和清水。
在其中一個實施例中,所述除油分散劑為聚合氯化鋁鐵、聚合氯化鋁、聚合氯化鐵或聚合硫酸鐵;所述除油分散劑的濃度為50mg/L~2000mg/L;所述高效助劑為聚丙烯酰胺;所述聚丙烯酰胺的濃度為6mg/L~200mg/L。
在其中一個實施例中,將所述含油浮渣經(jīng)脫水處理后進行油水分離,得到浮渣、污油和水的步驟具體為:
將所述含油浮渣進行脫水處理,得到浮渣和油水混合液;及
將所述油水混合液進行油水分離,得到污油和水。
在其中一個實施例中,在所述將含油污水進行油水分離的步驟之前還包括以下步驟:
將所述含油污水進行過濾。
上述含油污水處理裝置及方法,采用除油凈化裝置和浮渣分離裝置,先將含油污水進行油水分離,得到含油浮渣和清水,再將含油浮渣經(jīng)脫水處理后進行油水分離,得到浮渣、污油和水。含油污水中污油去除率可達96%以上,浮渣減量率在70%以上。