申請日2010.07.22
公開(公告)日2011.12.28
IPC分類號C02F9/10; C02F1/58; C02F1/38; C02F1/04
摘要
本發(fā)明針對含高濃度銨鹽和鈉鹽廢水,利用銨鹽與鈉鹽的溶解度隨溫度變化的特性差異,提供了一套蒸發(fā)濃縮結(jié)晶和冷卻結(jié)晶相結(jié)合的分離出高純度銨鹽與鈉鹽的工藝。本發(fā)明先將廢水進(jìn)行預(yù)處理,然后調(diào)節(jié)廢水中Cl-和NH4+的摩爾量關(guān)系,再通過高溫蒸發(fā)濃縮結(jié)晶和真空冷卻結(jié)晶分別回收高純度的鈉鹽和銨鹽。廢水經(jīng)蒸發(fā)冷凝后回用生產(chǎn)系統(tǒng),分離出的銨鹽與鈉鹽成為原料供工廠使用,做到了廢水資源的綜合利用與徹底治理,提高了工廠的經(jīng)濟(jì)效益與社會效益。本發(fā)明適用于濕法冶金企業(yè)與鹽化工企業(yè)中產(chǎn)生的含高濃度鈉鹽與銨鹽的廢水處理。
摘要附圖
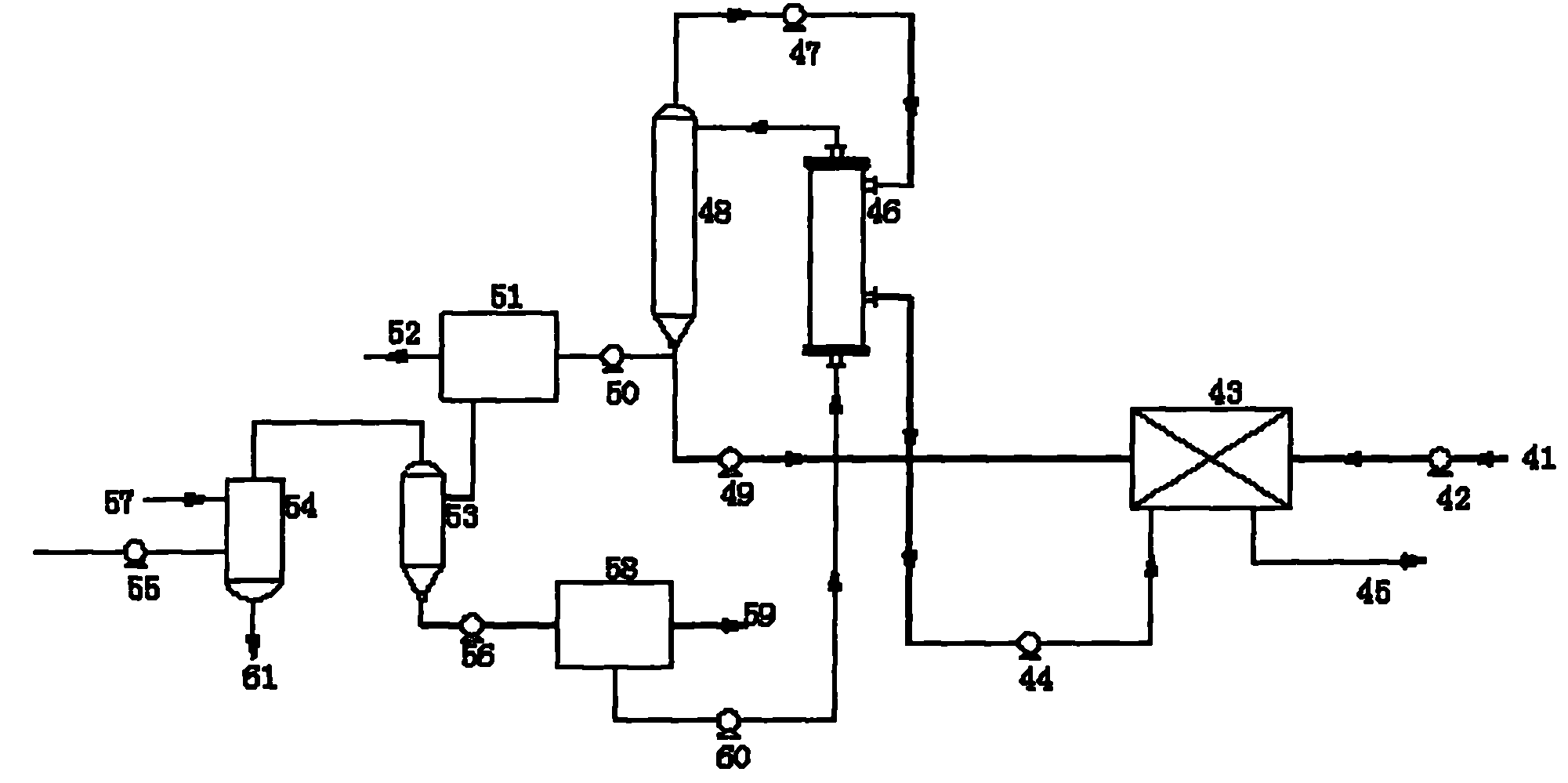
權(quán)利要求書
1.一種含銨鹽和鈉鹽廢水的處理工藝,包括以下步驟:
1)預(yù)處理:調(diào)節(jié)所述廢水的pH值為7.0-9.0后過濾,使廢水中懸浮物SS≤10mg/L, Ca2+離子濃度小于10mg/L;
2)蒸發(fā)結(jié)晶:使經(jīng)預(yù)處理后的廢水中CL-的摩爾量大于或等于NH4+的摩爾量,然后 送入蒸發(fā)濃縮系統(tǒng),控制結(jié)晶溫度為80-130℃,析出鈉鹽固體;
3)一級固液分離:從步驟2)所述蒸發(fā)濃縮系統(tǒng)中連續(xù)取出含鈉鹽固體的漿液進(jìn)行固 液分離得到固體鈉鹽;
4)冷卻結(jié)晶:將步驟3)固液分離后所得液體送入冷卻結(jié)晶系統(tǒng),控制結(jié)晶溫度為32-60 ℃,析出NH4Cl固體;
5)二級固液分離:將所述冷卻結(jié)晶系統(tǒng)產(chǎn)生的含NH4Cl固體的漿液進(jìn)行固液分離, 得到NH4Cl固體,所得液體返回所述蒸發(fā)濃縮系統(tǒng)。
2.如權(quán)利要求1所述的一種含銨鹽和鈉鹽廢水的處理工藝,其特征在于,所述含銨鹽和鈉 鹽廢水中包含NH4+和Na+,同時還包含Cl-和SO42-中的一種或兩種。
3.如權(quán)利要求1所述的一種含銨鹽和鈉鹽廢水的處理工藝,其特征在于,所述步驟1)中, 加入Na2CO3、NaHCO3、NH4HCO3或(NH4)2CO3,調(diào)節(jié)pH值及降低Ca2+的濃度。
4.如權(quán)利要求1所述的一種含銨鹽和鈉鹽廢水的處理工藝,其特征在于,所述步驟2)中, 當(dāng)預(yù)處理后的廢水中含有的Cl-的摩爾量大于NH4+的摩爾量時,將預(yù)處理后的廢水直 接送入蒸發(fā)濃縮系統(tǒng)中進(jìn)行結(jié)晶;當(dāng)預(yù)處理后的廢水中含有的Cl-的摩爾量小于NH4+的 摩爾量時,向所述廢水中加入NaCl,使Cl-的摩爾量和NH4+的摩爾量相等,然后再送 入蒸發(fā)濃縮系統(tǒng)中進(jìn)行結(jié)晶。
5.如權(quán)利要求1所述的一種含銨鹽和鈉鹽廢水的處理工藝,其特征在于,所述步驟3)中, 從蒸發(fā)濃縮系統(tǒng)中連續(xù)取出的含鈉鹽固體的漿液中,所述鈉鹽固體占所述漿液的重量百 分比為4-50%。
6.如權(quán)利要求1所述的一種含銨鹽和鈉鹽廢水的處理工藝,其特征在于,所述步驟3)中, 從蒸發(fā)濃縮系統(tǒng)中連續(xù)取出的含鈉鹽固體漿液的流量按照進(jìn)入所述蒸發(fā)濃縮系統(tǒng)的廢 水中所含氯化銨總量的3-10倍計算液體流量,所述銨鹽總量按廢水中所含的NH4+全部 形成氯化銨來計算,液體流量按比重1Kg/L計算。
7.如權(quán)利要求1所述的一種含銨鹽和鈉鹽廢水的處理工藝,其特征在于,所述步驟2)中, 廢水進(jìn)入蒸發(fā)濃縮系統(tǒng)之前,先預(yù)熱至50-70℃。
8.如權(quán)利要求1所述的一種含銨鹽和鈉鹽廢水的處理工藝,其特征在于,用水沖洗步驟3) 和步驟5)中所得的鈉鹽固體和NH4Cl固體,沖洗用水量小于固體鹽重量的20%。
9.如權(quán)利要求1-8中任一權(quán)利要求所述的一種含銨鹽和鈉鹽廢水的處理工藝,其特征在于, 所述蒸發(fā)濃縮系統(tǒng)為多效蒸發(fā)濃縮系統(tǒng)或熱泵蒸發(fā)濃縮系統(tǒng)。
10.如權(quán)利要求9所述的一種含銨鹽和鈉鹽廢水的處理工藝,其特征在于,當(dāng)所述蒸發(fā)濃縮 系統(tǒng)采用多效蒸發(fā)濃縮系統(tǒng)時:所述步驟2)中,預(yù)處理后的廢水先進(jìn)入預(yù)熱器中預(yù)熱, 再依次通過各效蒸發(fā)系統(tǒng),并于最后一效蒸發(fā)室內(nèi)進(jìn)行結(jié)晶,析出鈉鹽;所述預(yù)處理后 的廢水進(jìn)入的第一效蒸發(fā)室的溫度控制在55-80℃,最后一效蒸發(fā)室的溫度控制在 90-130℃。
11.如權(quán)利要求9所述的一種含銨鹽和鈉鹽廢水的處理工藝,其特征在于,當(dāng)所述蒸發(fā)濃縮 系統(tǒng)采用熱泵蒸發(fā)濃縮系統(tǒng)時,所述步驟2)中,預(yù)處理后的廢水先進(jìn)入預(yù)熱器中預(yù)熱, 再進(jìn)入所述熱泵蒸發(fā)濃縮系統(tǒng)中,并于其蒸發(fā)室內(nèi)進(jìn)行結(jié)晶,析出鈉鹽;所述熱泵蒸發(fā) 濃縮系統(tǒng)的蒸發(fā)室的溫度控制在90-130℃。
12.如權(quán)利要求1-8中任一權(quán)利要求所述的一種含銨鹽和鈉鹽廢水的處理工藝,其特征在于, 所述冷卻結(jié)晶系統(tǒng)為真空冷卻結(jié)晶系統(tǒng)或冷凍機(jī)組冷凍結(jié)晶系統(tǒng)。
13.如權(quán)利要求12所述的一種含銨鹽和鈉鹽廢水的處理工藝,其特征在于,所述真空冷卻 結(jié)晶系統(tǒng)包括由真空泵和冷凝器組成的真空冷凝系統(tǒng)和真空結(jié)晶罐;所述真空結(jié)晶罐的 蒸汽出口與冷凝器的入口經(jīng)管線連接;所述真空結(jié)晶罐內(nèi)設(shè)有機(jī)械攪拌裝置。
14.如權(quán)利要求1-8中任一權(quán)利要求所述的一種含銨鹽和鈉鹽廢水的處理工藝,其特征在于, 步驟3)與步驟5)中,所述固液分離均采用離心分離器進(jìn)行,所述離心分離器內(nèi)設(shè)有 水洗系統(tǒng)。
說明書
一種含高濃度銨鹽和鈉鹽廢水的處理工藝
技術(shù)領(lǐng)域
本發(fā)明涉及一種含高濃度銨鹽和鈉鹽廢水的處理工藝,尤其是涉及一種從含有氯化銨、 硫酸銨、氯化鈉和硫酸鈉的廢水中分別回收銨鹽與鈉鹽的工藝方法,屬于工業(yè)廢水處理領(lǐng) 域。
背景技術(shù)
濕法冶金過程排放的高濃度含銨鹽和鈉鹽廢水,目前主要處理工藝有下列幾種:
1、加堿(NaOH或Ca(OH)2)脫氨,治理不徹底。
2、蒸發(fā)濃縮后冷凍結(jié)晶,此時結(jié)晶物為銨鹽和鈉鹽的混合物,成固廢物處理。
3、加堿脫氣中吸收氨成氨水回用,廢水蒸發(fā)濃縮處理。
這些方法雖然治理了廢水,但又多了一項固體廢棄物,運(yùn)行成本高,一噸廢水的處理 費(fèi)用超過20元人民幣。
中國專利200910068695.6公開了從制堿母液中回收氯化銨和氯化鈉,采用多效真空蒸 發(fā)濃縮結(jié)晶析出氯化鈉與氯化銨,這種廢水不含硫酸根。
中國發(fā)明專利200910010988.9公開了含有氨、釩、鉻和硫酸鈉廢水處理的方法,此方 法采用加堿脫氨氣法處理銨鹽、堿液耗量大,運(yùn)行成本高。
發(fā)明內(nèi)容
本發(fā)明的目的在于克服現(xiàn)有技術(shù)中的不足之處,提供一種綜合處理含高濃度銨鹽和鈉 鹽的工藝,分別回收銨鹽和鈉鹽,使廢水處理資源化,最大限度地減少二次污染,提高經(jīng) 濟(jì)效益和社會效益。
本發(fā)明利用銨鹽與鈉鹽的溶解度隨溫度變化的特性差異,針對含高濃度銨鹽和鈉鹽的廢 水,提供了一套蒸發(fā)濃縮結(jié)晶和冷卻結(jié)晶相結(jié)合的分離高純度銨鹽與鈉鹽的工藝,采用的 技術(shù)方案如下:
一種含高濃度銨鹽和鈉鹽廢水的處理工藝,包括以下步驟:
1)預(yù)處理:調(diào)節(jié)所述廢水的pH值為7.0-9.0后過濾,使廢水中懸浮物SS≤10mg/L, Ca2+離子濃度小于10mg/L,以防止蒸發(fā)結(jié)晶時設(shè)備結(jié)垢;
2)蒸發(fā)結(jié)晶:使經(jīng)預(yù)處理后的廢水中Cl-的摩爾量大于或等于NH4+的摩爾量,然后 送入蒸發(fā)濃縮系統(tǒng),控制結(jié)晶溫度為80-130℃,析出鈉鹽固體;
3)一級固液分離:從步驟2)所述蒸發(fā)濃縮系統(tǒng)中連續(xù)取出含鈉鹽固體的漿液進(jìn)行固 液分離得到固體鈉鹽;
4)冷卻結(jié)晶:將步驟3)固液分離后所得液體送入冷卻結(jié)晶系統(tǒng),控制結(jié)晶溫度為32-60 ℃,析出NH4Cl固體;
5)二級固液分離:將所述冷卻結(jié)晶系統(tǒng)產(chǎn)生的含NH4Cl固體的漿液進(jìn)行固液分離, 得到NH4Cl固體,所得液體返回所述蒸發(fā)濃縮系統(tǒng)。
所述廢水為濕法冶金生產(chǎn)釩、鎳、鈷、鋰等金屬過程中產(chǎn)生的廢水,也可以為其他化工 工業(yè)生產(chǎn)排放的類似廢水,其中包含NH4+和Na+,同時還包含Cl-和SO42-中的一種或兩種。 即,其中含有氯化銨、硫酸銨、氯化鈉、硫酸鈉等物質(zhì)。所述廢水中含有的銨鹽(氯化銨 和/或硫酸銨總量)的濃度大于1g/L;優(yōu)選的,所述廢水中含有的銨鹽(氯化銨和/或硫酸銨 總量)的濃度大于10g/L。
較佳的,所述步驟1)中加入Na2CO3、NaHCO3、NH4HCO3或(NH4)2CO3調(diào)節(jié)pH 值及降低Ca2+的濃度。
步驟2)中,當(dāng)預(yù)處理后的廢水中含有的Cl-的摩爾量大于NH4+的摩爾量時,將預(yù)處 理后的廢水直接送入蒸發(fā)濃縮系統(tǒng)中進(jìn)行結(jié)晶,此時析出的鈉鹽為氯化鈉和硫酸鈉的混合 物;當(dāng)預(yù)處理后的廢水中含有的Cl-的摩爾量小于NH4+的摩爾量時,向所述廢水中加入 NaCl,使Cl-的摩爾量和NH4+的摩爾量相等,然后再送入蒸發(fā)濃縮系統(tǒng)中進(jìn)行結(jié)晶,此時 析出的鈉鹽為硫酸鈉。
本發(fā)明所提供的上述含高濃度銨鹽和鈉鹽廢水的處理工藝,為連續(xù)操作過程。
較佳的,所述步驟3)中,從蒸發(fā)濃縮系統(tǒng)中連續(xù)取出的含鈉鹽固體的漿液中,所述鈉 鹽固體占所述漿液的重量百分比為4-50%
較佳的,所述步驟3)中,從蒸發(fā)濃縮系統(tǒng)中連續(xù)取出的含鈉鹽固體漿液的流量按照進(jìn) 入所述蒸發(fā)濃縮系統(tǒng)的廢水中所含銨鹽(氯化銨,即按廢水中所含的NH4+全部形成氯化銨 來計算)總量的3-10倍計算液體流量(液體流量按比重1Kg/L計算)。
較佳的,所述步驟2)中,廢水進(jìn)入蒸發(fā)濃縮系統(tǒng)之前,先進(jìn)入預(yù)熱器中預(yù)熱至50-70 ℃。
較佳的,用水沖洗步驟3)和步驟5)中所得的鈉鹽固體和NH4Cl固體,以提高其純度, 沖洗用水量小于固體鹽重量的20%,優(yōu)選為固體鹽重量的5-20%。
本發(fā)明的上述方法通過控制廢水中的Cl-和NH4+間的比例關(guān)系,以及先通過高溫蒸發(fā) 結(jié)晶,再通過低溫冷卻結(jié)晶的工藝處理過程,將廢水中的鈉鹽和銨鹽分別分離出來。其中, 所采用的各種設(shè)備包括蒸發(fā)濃縮系統(tǒng)和冷卻結(jié)晶系統(tǒng)等,均可使用本領(lǐng)域內(nèi)的常規(guī)結(jié)晶設(shè) 備與裝置。如:所述蒸發(fā)濃縮系統(tǒng)可以是一效蒸發(fā)系統(tǒng)、二效蒸發(fā)系統(tǒng)、三效蒸發(fā)系統(tǒng)或 四效蒸發(fā)系統(tǒng)等多效蒸發(fā)濃縮系統(tǒng),也可以是熱泵蒸發(fā)濃縮系統(tǒng)。通常多效蒸發(fā)系統(tǒng)級數(shù) 越多,蒸發(fā)一噸水所需蒸汽越少,但是其設(shè)備投資和電力消耗會增大。為降低綜合能耗, 優(yōu)選三效蒸發(fā)系統(tǒng)、四效蒸發(fā)系統(tǒng)或熱泵蒸發(fā)濃縮系統(tǒng)。
當(dāng)所述蒸發(fā)濃縮系統(tǒng)采用多效蒸發(fā)濃縮系統(tǒng)時,所述步驟2)中,預(yù)處理后的廢水先進(jìn) 入預(yù)熱器中預(yù)熱,再依次通過各效蒸發(fā)系統(tǒng),并于最后一效蒸發(fā)室內(nèi)進(jìn)行結(jié)晶,析出鈉鹽。
較佳的,所述預(yù)處理后的廢水進(jìn)入的第一效蒸發(fā)室的溫度控制在55-80℃,屬于負(fù)壓蒸 發(fā);最后一效蒸發(fā)室的溫度控制在90-130℃,可以選擇負(fù)壓或正壓蒸發(fā)。
當(dāng)所述蒸發(fā)濃縮系統(tǒng)采用熱泵蒸發(fā)濃縮系統(tǒng)時,所述步驟2)中,預(yù)處理后的廢水先進(jìn) 入預(yù)熱器中預(yù)熱,再進(jìn)入所述熱泵蒸發(fā)濃縮系統(tǒng)中,并于其蒸發(fā)室內(nèi)進(jìn)行結(jié)晶,析出鈉鹽。
較佳的,所述熱泵蒸發(fā)濃縮系統(tǒng)的蒸發(fā)室的溫度控制在90-130℃,可以選擇負(fù)壓或正壓 蒸發(fā)。
本發(fā)明所提供的方法中,所述冷卻結(jié)晶系統(tǒng)可以是真空冷卻結(jié)晶系統(tǒng)或冷凍機(jī)組冷凍結(jié) 晶系統(tǒng)。本發(fā)明優(yōu)選真空冷卻結(jié)晶系統(tǒng),以降低綜合能耗。
所述真空冷卻結(jié)晶系統(tǒng)包括由真空泵和冷凝器組成的真空冷凝系統(tǒng)和真空結(jié)晶罐;所述 真空結(jié)晶罐的蒸汽出口與冷凝器的入口經(jīng)管線連接。
較佳的,所述真空結(jié)晶罐內(nèi)的溫度控制在35-60℃。
較佳的,所述真空冷卻結(jié)晶系統(tǒng)連續(xù)工作,通過由真空結(jié)晶罐底部連續(xù)采出一定量的含 結(jié)晶固體的溶液,控制真空結(jié)晶罐內(nèi)的液位維持在一定的高度。
較佳的,所述真空結(jié)晶罐內(nèi)設(shè)有機(jī)械攪拌裝置,防止銨鹽在內(nèi)壁結(jié)晶,并能使銨鹽結(jié)晶 體粒徑小于0.5mm,小晶體不容易損壞循環(huán)泵葉輪。
本發(fā)明所提供的方法中,步驟3)與步驟5)中,所述固液分離均采用離心分離器進(jìn)行, 所述離心分離器內(nèi)設(shè)有水洗系統(tǒng)。
與現(xiàn)有技術(shù)相比,本發(fā)明的創(chuàng)新之處主要在于:針對含高濃度銨鹽和鈉鹽的廢水,通過 調(diào)整廢水中的Cl-和NH4+間的比例關(guān)系,以及采用高溫蒸發(fā)結(jié)晶和低溫冷卻結(jié)晶相結(jié)合的 工藝處理過程,使廢水中的銨鹽與鈉鹽分別回收;厥盏拟c鹽和銨鹽可作為工業(yè)應(yīng)用的原 料和農(nóng)業(yè)肥料,同時廢水經(jīng)蒸發(fā)冷凝后可回用生產(chǎn)系統(tǒng)。治廢的同時,做到資源綜合回收 利用,達(dá)到無廢水和固體廢棄物排放,提高了工廠的經(jīng)濟(jì)效益與社會效益。本發(fā)明適用于 濕法冶金企業(yè)與鹽化工企業(yè)的高含銨廢水處理。