申請日2010.06.25
公開(公告)日2011.12.28
IPC分類號C02F1/40
摘要
本發(fā)明涉及一種處理廢水中重質(zhì)乳化油的方法;處理裝置為下部鼓泡段為氣升式內(nèi)環(huán)流反應(yīng)器,上部泡沫段為溢流槽式的氣液分離器;調(diào)節(jié)廢水的pH為8~9,將廢水通入鼓泡段;在塔底通入空氣,加入絮凝劑和表面活性劑;通過收集泡沫,將乳化油從廢水中分離;無機(jī)絮凝劑用量為:0.02~0.1mmol/g COD;聚合物絮凝劑用量為:10~50mg/m3廢水;陰離子表面活性劑,用量為:5~20mg/g COD,且不低于15~20mg/m3廢水;保持空塔氣速為0.5~1.5cm/s;分離效率高:一次分離率可達(dá)90%以上;工藝過程簡單:廢水一次通過脫除固體懸浮物;能耗和劑耗低:絮凝劑用量低,流程短。
摘要附圖
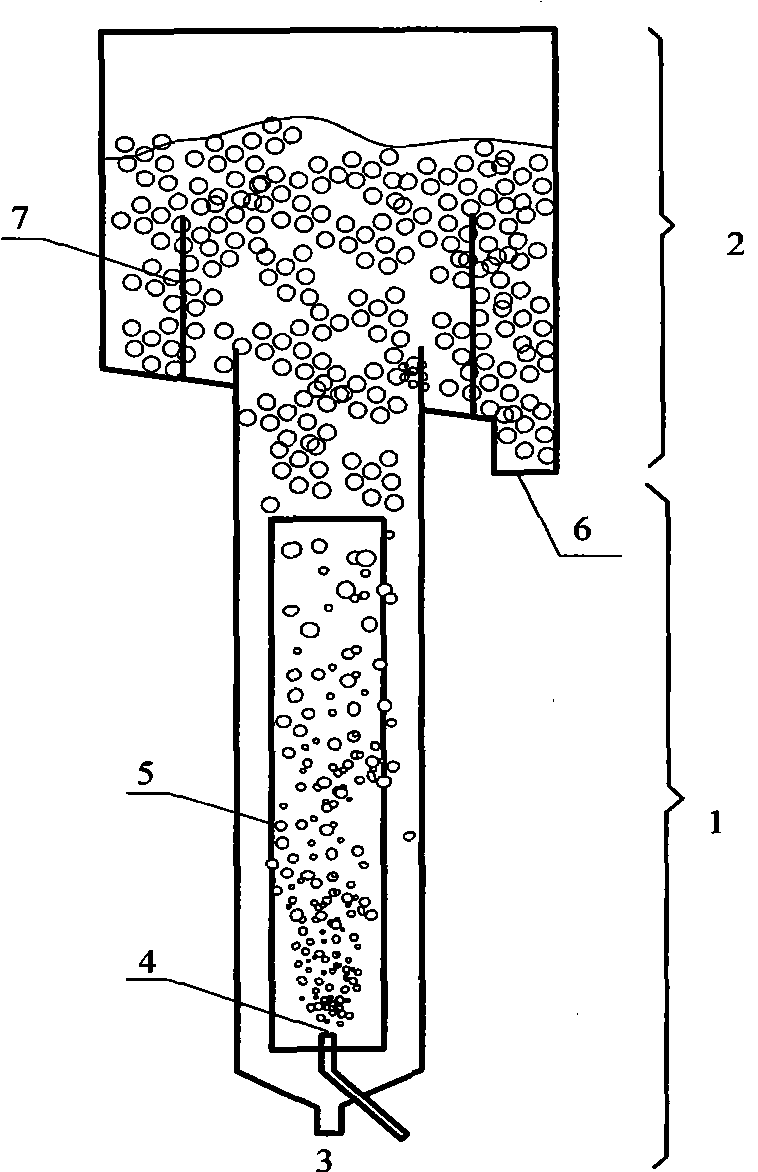
權(quán)利要求書
1.一種處理廢水中重質(zhì)乳化油的方法,其特征在于:
處理裝置為一種由鼓泡段和泡沫段構(gòu)成的環(huán)流泡沫分離塔,下部鼓泡段為氣升式 內(nèi)環(huán)流反應(yīng)器,上部泡沫段為溢流槽式的氣液分離器;調(diào)節(jié)廢水的pH為8~9,將廢 水通入環(huán)流泡沫分離塔的鼓泡段;在塔底通入空氣,加入絮凝劑和表面活性劑;表面 活性劑產(chǎn)生泡沫,使絮凝的乳化油滴富集在泡沫表面,通過收集泡沫,將乳化油從廢 水中分離;
所述絮凝劑由無機(jī)絮凝劑和聚合物絮凝劑構(gòu)成;無機(jī)絮凝劑用量為:0.02~0.1 mmol/g COD;聚合物絮凝劑用量為:10~50mg/m3廢水;
所述表面活性劑為陰離子表面活性劑,其用量為:5~20mg/g COD,且不低于15 ~20mg/m3廢水;
所述的空氣通入量為:保持空塔氣速為0.5~1.5cm/s。
2.根據(jù)權(quán)利要求1所述的處理廢水中重質(zhì)乳化油的方法,其特征在于:無機(jī)絮凝 劑為氯化鋁、硫酸鋁、硫酸亞鐵、三氯化鐵、氯化鈣;聚合物絮凝劑為聚丙烯酰胺。
3.根據(jù)權(quán)利要求1所述的處理廢水中重質(zhì)乳化油的方法,其特征在于:可選擇 十二烷基磺酸鈉、十二烷基硫酸鈉中的一種或其組合。
4.根據(jù)權(quán)利要求1所述的處理廢水中重質(zhì)乳化油的方法,其特征在于:所述環(huán)流 泡沫分離塔鼓泡段和泡沫段的直徑比為1∶(1.4~1.8),高度比為1∶(0.4~0.8);泡沫 段溢流槽堰和鼓泡段直徑比為(1~1.4)∶1,溢流槽堰和泡沫段的高度比為(0.1~0.3)∶1。 鼓泡段中的導(dǎo)流筒可為單級或多級導(dǎo)流筒。
說明書
處理廢水中重質(zhì)乳化油的方法
技術(shù)領(lǐng)域
本發(fā)明涉及一種從原油加工廢水中脫除重質(zhì)乳化油的方法。
背景技術(shù)
重質(zhì)原油即稠油加工過程會(huì)產(chǎn)生大量含有重質(zhì)乳化油的廢水,包括原油罐底脫 水、脫鹽脫鈣污水、焦化大吹汽冷凝水等,這種水與普通煉油廢水、油田廢水相比, 其突出特點(diǎn)是:①乳化油含量高:一般情況下,重質(zhì)原油加工廢水中一半以上的油以 乳化油形式存在,除去浮油和分散油后,80%以上的COD是由于乳化油和膠態(tài)懸浮 物產(chǎn)生的;②乳化程度嚴(yán)重,乳滴穩(wěn)定:重質(zhì)乳化油的乳滴直徑通常只有幾百納米 到幾微米,由于廢水中存在著采油過程中引入的大量界面活性物質(zhì)以及大量的膠質(zhì)、 瀝青質(zhì)的懸浮物,使得乳滴非常穩(wěn)定;③乳化油粘度大:重質(zhì)原油的粘度大,其100 ℃的運(yùn)動(dòng)粘度可達(dá)到100mm2/s以上,高粘度使乳滴界面異常穩(wěn)定,流動(dòng)性變差,造 成乳滴不易聚并和吸附;④乳化油密度大:重質(zhì)原油的密度與水接近,因此通過沉降 方法分離油水的效率非常低,即使絮凝后的乳化油與水分離效果仍然較差。
由于重質(zhì)乳化油含量高,且難以被生物降解,因此在進(jìn)入生化處理前,必須先采 用物理和化學(xué)的方法進(jìn)行預(yù)處理,而預(yù)處理的核心環(huán)節(jié)就是脫除浮化油。目前,脫除 浮化油方法包括吸附、萃取、絮凝沉降、氣浮、膜分離等,其中絮凝沉降和氣浮方法 比較常見,由于重質(zhì)原油的密度高、粘度大,絮凝后的乳化油相分離不好,沉降分離 時(shí)間長、效率低,因而采用上述單一方法進(jìn)行重油乳化油脫除效果很不理想;若經(jīng)絮 凝沉降分離后,進(jìn)一步采用氣浮等手段分離未沉降分離的乳化油,又存在過程復(fù)雜、 能耗高缺陷。如陳春茂等在2007年第4期《煉油技術(shù)與工程》“遼河石化超稠油污 水預(yù)處理工藝與工程實(shí)踐”中報(bào)道的采用水質(zhì)水量調(diào)節(jié)—破乳除油—旋流油水分離— 浮選凈化工藝對超稠油污水預(yù)處理的方法。
由于乳化程度高,乳滴非常小且異常穩(wěn)定,而穩(wěn)定的油滴在氣泡界面的吸附量非 常小,因此需要大量的氣泡界面吸附乳滴,需要多級氣浮以達(dá)到需要的分離效果,從 而導(dǎo)致氣浮分離能耗高且分離效率低,例如CN101327966公開的一種稠油污水射流 溶氣氣浮工藝,包括一次氣浮、射流溶氣、二次氣浮等在內(nèi)的多級分離技術(shù)。
近年來,一些新的高效氣浮分離設(shè)備和技術(shù)被報(bào)道,如US 2008/0006588公開的 氣旋浮選分離技術(shù),CN 1546196公開的加壓溶氣氣浮水力旋流油水分離的方法和裝 置,其采用氣浮脫油和旋流分離結(jié)合方式對含油廢水料液進(jìn)行脫油,上述文獻(xiàn)均沒有 報(bào)道對重質(zhì)乳化油廢水的分離效果。
US 5897772公開了一種多級環(huán)流泡沫分離塔等。多級環(huán)流泡沫分離塔是一種在 環(huán)流反應(yīng)器基礎(chǔ)上開發(fā)的氣浮分離設(shè)備。由于氣浮分離的效率很大程度上取決于氣泡 與連續(xù)相充分、快速的接觸,與一般的氣浮設(shè)備相比,環(huán)流反應(yīng)器內(nèi)氣泡快速湍動(dòng), 氣液接觸充分,可使被分離的物質(zhì)較快的富集在泡沫表面上,因而能顯著提高泡沫分 離的效率。實(shí)驗(yàn)證實(shí),該技術(shù)對于大小在10μm以上的乳化油有較高的分離效率。對 粒徑更小、界面流動(dòng)性差的重質(zhì)油乳滴沒有顯著的分離效果,這是因?yàn)槿榛w系的穩(wěn) 定性提高,乳滴的界面性質(zhì)發(fā)生很大變化,界面電荷相斥,很難僅通過泡沫分離的技 術(shù)將乳滴聚集分離,必須先采用其他技術(shù)使乳滴直徑增加,表面性質(zhì)改善而利于泡沫 分離。
CN1435275A在傳統(tǒng)鼓泡式反應(yīng)器基礎(chǔ)上公開了一種多級環(huán)流反應(yīng)器,塔內(nèi)置有 導(dǎo)流筒,導(dǎo)流筒底部設(shè)有氣體分布器,該反應(yīng)器可廣泛用于氧化反應(yīng)、發(fā)酵過程、烴 加工反應(yīng)以及活性污泥污水處理過程等各類氣-液或氣-液-固化學(xué)反應(yīng)過程當(dāng)中。
發(fā)明內(nèi)容
本發(fā)明的目的在于提供一種利用環(huán)流泡沫分離塔分離脫除重質(zhì)原油加工廢水中 乳化油的方法。本方法是在多級環(huán)流泡沫分離塔和環(huán)流反應(yīng)器及多級環(huán)流反應(yīng)器的基 礎(chǔ)上,結(jié)合絮凝技術(shù),針對粒徑在10μm以下的乳化重質(zhì)油滴,開發(fā)出的一種絮凝- 環(huán)流泡沫分離處理乳化油的方法,可提高重質(zhì)乳化油分離效率,簡化分離流程。
本發(fā)明所述的處理廢水中重質(zhì)乳化油的方法是通過如下技術(shù)方案實(shí)現(xiàn)的:
處理裝置為一種由鼓泡段和泡沫段構(gòu)成的環(huán)流泡沫分離塔,下部鼓泡段為氣升式 內(nèi)環(huán)流反應(yīng)器,上部泡沫段為溢流槽式的氣液分離器;調(diào)節(jié)廢水的pH為8~9,將廢 水通入環(huán)流泡沫分離塔的鼓泡段;在塔底通入空氣,加入絮凝劑(由無機(jī)絮凝劑和聚 合物絮凝劑組成)和表面活性劑;表面活性劑產(chǎn)生泡沫,使絮凝的乳化油滴富集在泡 沫表面,通過收集泡沫,將乳化油從廢水中分離。
所述環(huán)流泡沫分離塔由下部鼓泡段和上部泡沫段構(gòu)成,由于多級環(huán)流泡沫塔的鼓 泡段相當(dāng)于一種多級環(huán)流反應(yīng)器,因此本發(fā)明的分離塔下部鼓泡段成為一種氣升式內(nèi) 環(huán)流反應(yīng)器,上部泡沫段為溢流槽式的氣液分離器。具體地說,環(huán)流泡沫分離塔,由 鼓泡段1和泡沫段2構(gòu)成,鼓泡段1為氣升式內(nèi)環(huán)流反應(yīng)器,包括導(dǎo)流筒5和氣體分 布器4,其中多級導(dǎo)流筒或單級導(dǎo)流筒,單級導(dǎo)流筒為導(dǎo)流筒的常規(guī)設(shè)計(jì),多級導(dǎo)流 筒按照專利CN1435275設(shè)計(jì),專利CN1435275一種用于各類氣-液兩相和氣-液-固三 相化學(xué)反應(yīng)多級環(huán)流反應(yīng)器,包括塔身、導(dǎo)流筒、氣體分布器,塔身內(nèi)有導(dǎo)流筒,導(dǎo) 流筒的底部有氣體分布器,塔身總高與反應(yīng)器內(nèi)徑之比為3~12,導(dǎo)流筒直徑與反應(yīng) 器內(nèi)徑之比為0.3~0.9。泡沫段位于鼓泡段上方,為溢流槽式氣液分離器,有溢流堰 7和泡沫排出口6。環(huán)流泡沫分離塔鼓泡段和泡沫段的直徑比為1∶1.4~1∶1.8,高度比 為1∶0.4~1∶0.8;泡沫段溢流槽堰和鼓泡段直徑的比為1∶1~1.4∶1,溢流槽堰和泡沫段的 高度比為0.1∶1~0.3∶1。所述的廢水為含有重質(zhì)原油加工過程中產(chǎn)生含有的重質(zhì)乳化 油的廢水,乳滴在2~10μm范圍內(nèi),乳化油產(chǎn)生的COD占廢水總COD的75%~95%, 包括但不限于油罐底脫水、脫鹽脫鈣污水、油田超稠油污水、焦化大吹汽冷凝水。
所述的絮凝劑由無機(jī)絮凝劑和聚合物絮凝劑組成,其中無機(jī)絮凝劑為氯化鋁、硫 酸鋁、硫酸亞鐵、三氯化鐵、氯化鈣,常規(guī)無機(jī)鋁、鐵、鈣鹽絮凝劑用量為(乳化油 按COD計(jì)量,絮凝劑按所含金屬離子的物質(zhì)的量計(jì)量):(0.02~0.1)mmol/g COD; 聚合物絮凝劑為聚丙烯酰胺,其用量為:10~50mg/m3廢水。所述表面活性劑為陰離 子表面活性劑,可選擇十二烷基磺酸鈉、十二烷基硫酸鈉中的一種或其組合,其用量 為和乳化油含量滿足(乳化油按COD計(jì)量):5~20mg/g COD乳化油,且不低于 15~20mg/m3廢水。
所述通入空氣的量為:保持空塔氣速為0.5~1.5cm/s。
本發(fā)明的絮凝-環(huán)流泡沫分離廢水中重質(zhì)乳化油的方法,可采用連續(xù)操作,也可 采取批式操作。
批式操作:廢水一次性泵入環(huán)流泡沫分離塔鼓泡段,液面高度不低于導(dǎo)流筒上沿, 且和導(dǎo)流筒上沿高度的比為1∶1~1∶1.25,用酸堿調(diào)節(jié)pH為8~9;從氣體分布器通入空 氣,通氣量保證空塔氣速為0.5~1.5cm/s;分別緩慢流加無機(jī)絮凝劑水溶液(濃度為 飽和濃度5%~25%)和聚合物絮凝劑聚丙烯酰胺的水溶液(濃度為25~250mg/L); 表面活性劑配置成一定濃度(為臨界膠束濃度10%~40%)的水溶液,存儲在儲罐中, 待絮凝過程發(fā)生后,開始用計(jì)量泵以恒定速率流加表面活性劑溶液到鼓泡段任意位 置,表面活性劑用量為5~20mg/g COD,且不低于15~20mg/m3廢水,流加速率根 據(jù)用量和溶液濃度以及分離總時(shí)間的確定;同時(shí)開始從泡沫段底部的泡沫收集口6 收集泡沫,當(dāng)乳化油的脫除率達(dá)到排放要求后,完成一個(gè)批次的操作。
連續(xù)操作:環(huán)流泡沫塔中通入空氣,保證空塔氣速為0.5~1.5cm/s,廢水事先用 酸堿調(diào)節(jié)pH為8~9,然后以通過泵8泵入環(huán)流泡沫分離塔的鼓泡段,水力停留時(shí)間 為0.5~2h,進(jìn)料速率根據(jù)水力停留時(shí)間確定,進(jìn)料口可在鼓泡段的任意位置;表面 活性劑、無機(jī)絮凝劑、聚合物絮凝劑配置成一定濃度的水溶液(無機(jī)絮凝劑濃度為飽 和濃度5%~25%,聚合物絮凝劑濃度為25~250mg/L,表面活性劑濃度為臨界膠束濃 度10%~40%,),分別儲存在不同的儲罐9、10、11中,用計(jì)量泵12以恒定速率流加 到鼓泡段任意位置,流加速率根據(jù)用量、溶液的濃度和液相的停留時(shí)間確定;從泡沫 收集口連續(xù)收集泡沫而收集乳化油;從鼓泡段底部排液口3排出脫除乳化油后的廢 水,整個(gè)操作過程中保證塔內(nèi)裝液量不變。
本發(fā)明原理:在含乳化油污水中,添加一定類型和一定量的絮凝助劑,將乳滴聚 集成一定大小,中和乳滴上的部分表面電荷,改善乳滴的表面性質(zhì),降低乳化體系的 穩(wěn)定性,使用與絮凝助劑配合的表面活性劑形成泡沫,使聚集長大的乳滴高效的吸附 在泡沫相中從而被分離。本發(fā)明中所謂的“控制絮凝”并不形成絮凝相,而是使油滴 長大,達(dá)到泡沫分離較好的范圍,然后用泡沫進(jìn)行分離。
本發(fā)明的優(yōu)點(diǎn)和有益效果是:
分離效率高:采用控制絮凝的方法,使乳化油的直徑增加,界面性質(zhì)改變,并中 和了部分界面電荷,從而滿足了泡沫分離的要求,再結(jié)合采用高效的環(huán)流泡沫分離, 重質(zhì)乳化油的一次分離率可達(dá)90%以上。
工藝過程簡單:廢水一次通過環(huán)流泡沫分離塔,即可實(shí)現(xiàn)乳化油和固體懸浮物的 脫除,脫油后的污水可直接進(jìn)行生化處理,使重質(zhì)原油加工廢水的處理工藝和過程簡 化。
能耗和劑耗低:絮凝劑的用量低于傳統(tǒng)的絮凝-沉降分離方法,同時(shí)由于縮短了 工藝流程,也就避免了廢水在各處理單元的傳輸和循環(huán),降低了能耗。