申請日2010.06.25
公開(公告)日2011.01.05
IPC分類號C01B31/02
摘要
含油污泥熱解殘渣中碳分離回收的方法,應用于采油廢水與油泥污染處理技術領域。熱解殘渣和活化劑同時進入攪拌機攪拌均勻;然后進入活化反應爐活化處理1~4小時;利用補水系統(tǒng)將活化后殘渣沖入第一反應罐中并加試液A;活化后熱解殘渣與試液A質量比為1∶2~1∶15;通蒸汽,水漂洗殘渣3~8次;殘渣沖入第二反應罐7內(nèi)并加入試液B,經(jīng)試液A處理工序后熱解殘渣與試液B質量比為1∶3~1∶12;通入蒸汽;殘渣沖入貯碳槽,開動貯碳槽攪拌器,碳與水混合;開動離心機脫水;進入干式球磨機粉碎到120~200目。效果是:分離回收效果好;占地面積小;操作方便;經(jīng)濟可行,無二次污染,能回收碳資源,能耗低,運行成本低。
摘要附圖
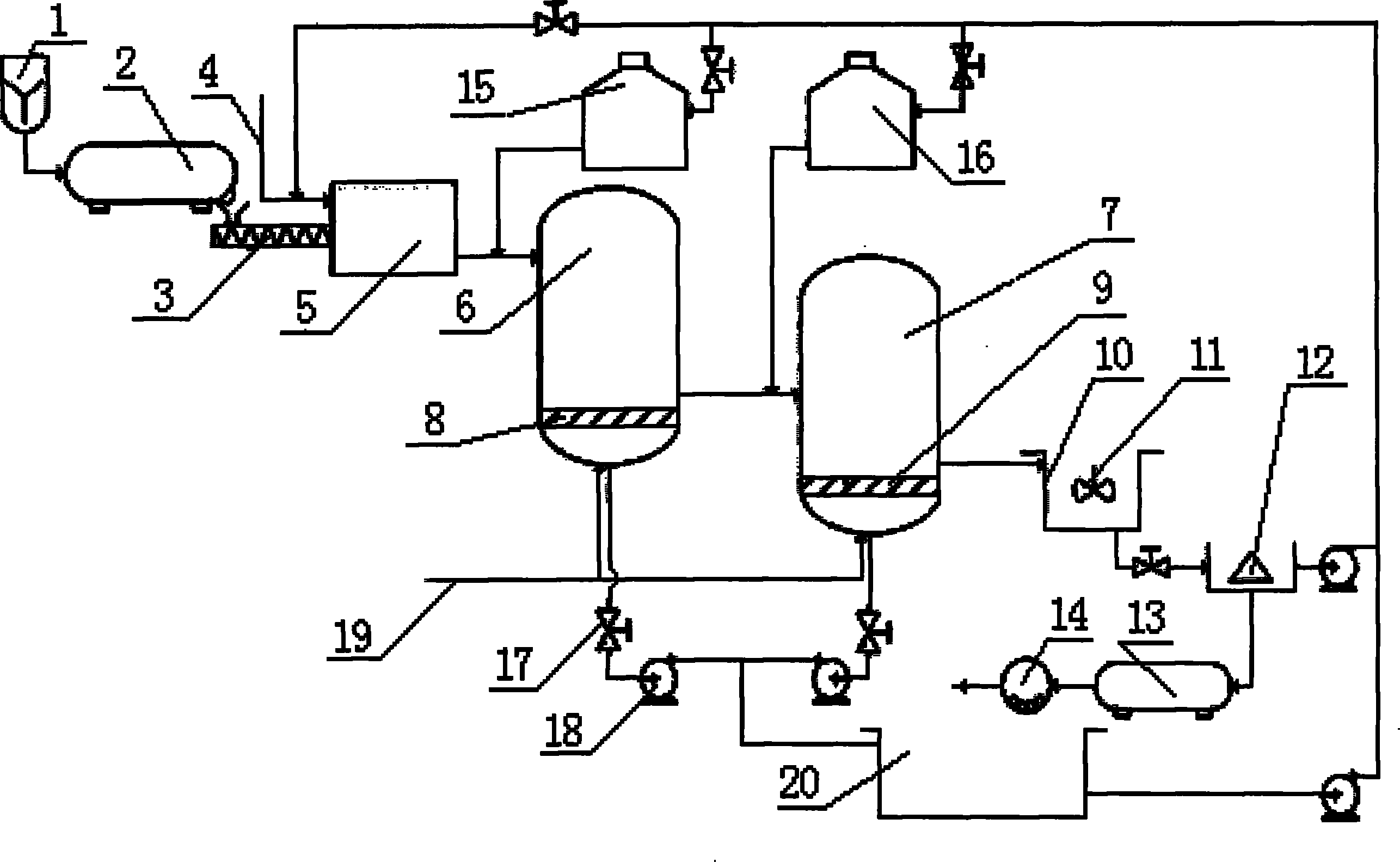
權利要求書
1.一種含油污泥熱解殘渣中碳分離回收的方法,其特征在于:
A、熱解殘渣和活化劑同時加入攪拌機(1)攪拌均勻,熱解殘渣與活化劑的質量比為1∶2~1∶4;活化劑是氯化物溶液和硫化物溶液的混合液,其中氯化物含有銨、鈉、鐵、鋁、鋅、硼、鎂、錳或鈣中的一種陽離子,優(yōu)選氯化鋅;硫化物含有鈉或鉀中的一種陽離子,優(yōu)選硫化鉀,氯化物溶液與硫化物溶液的體積比為1∶0.3~1∶0.45,氯化物溶液與硫化物溶液的濃度均為3mol/L;
B、然后將熱解殘渣和活化劑送入活化反應爐(2)進行活化處理,升溫速度:5~10℃/min,活化處理的溫度在400~900℃,活化處理的時間為1~4小時,在活化反應爐(2)內(nèi)形成活化后熱解殘渣;
C、將活化后熱解殘渣通過螺旋輸送機(3)輸送入回收桶(5)中,利用回收桶(5)與第一反應罐(6)的高度差,并利用補水系統(tǒng)(4)的水將活化后熱解殘渣沖入第一反應罐(6)中;
D、同時利用第一加藥罐(15)往第一反應罐(6)內(nèi)加入試液A,活化后熱解殘渣與試液A質量比為1∶2~1∶15;試液A是硫酸溶液、鹽酸溶液、磷酸溶液和氫氟酸溶液中一種或兩種的混合物,濃度為1~8mol/L;
E、通過蒸氣管道(19)往第一反應罐(6)內(nèi)通入120℃蒸汽20~60分鐘;開啟第一反應罐(6)底部過濾板A(8)放出第一反應罐(6)內(nèi)的廢液,用水漂洗殘渣3~8次,用泵(18)將廢液和漂洗廢水打入廢液儲存池(20)儲存,儲存池上清液返回補水系統(tǒng)(4)或第一加藥罐(15)或第二加藥罐(16)再使用;
F、將第一反應罐(6)內(nèi)經(jīng)試液A處理工序后熱解殘渣用水沖入第二反應罐(7)內(nèi);同時利用第二加藥罐(16)向第二反應罐(7)內(nèi)加入試液B,經(jīng)試液A處理工序后熱解殘渣與試液B的質量比為1∶3~1∶12;試液B為氫氧化鈉溶液、氫氧化鉀溶液中的一種,試液B重量百分比濃度為1%~15%;通入120℃蒸汽20~40分鐘;開啟第二反應罐(7)底部過濾板B(9)放出第二反應罐(7)內(nèi)的廢液,用水漂洗殘渣3~8次至溶液呈中性,用泵將廢液和漂洗廢水打入廢液儲存池(20)儲存,儲存池上清液返回補水系統(tǒng)(4)或第一加藥罐(15)或第二加藥罐(16)再使用;
G、將第二反應罐7內(nèi)經(jīng)試液B處理工序后熱解殘渣從第二反應罐(7)沖入貯碳槽(10)中;然后開動貯碳槽(10)內(nèi)的攪拌器(11),使漂洗碳與水混合;
H、將漂洗碳和水通過貯碳槽(10)底部閥門進入離心機(12)進行脫水,液體通過泵返回補水系統(tǒng)(4)或第一加藥罐(15)或第二加藥罐(16)循環(huán)使用;脫水后的濕碳輸送入回轉干燥機(13)進行干燥處理,干燥后的碳送入干式球磨機(14)粉碎到120~200目。
2.根據(jù)權利要求1所述的含油污泥熱解殘渣中碳分離回收的方法,其特征是:使用的裝置是由攪拌機(1)、活化反應爐(2)、螺旋輸送機(3)、反應罐、加藥罐、蒸氣管道(19)、過濾板、貯碳槽(10)、離心機(12)、干燥機(13)、球磨機(14)和廢液儲存池(20)組成,攪拌機(1)出口與活化反應爐(2)入口連接,活化反應爐(2)出口安裝有螺旋輸送機(3);螺旋輸送機(3)的出口連接回收桶(5)的進料口;
回收桶(5)與補水系統(tǒng)(4)連接,回收桶(5)下部出料口有管線與第一反應罐(6)上部進料口連接,在回收桶(5)和第一反應罐(6)之間的管線上通過三通和管線連接加藥罐A(15)的出口;第一反應罐(6)下部連接有蒸氣管道(19),第一反應罐(6)內(nèi)底部有過濾廢液的過濾板A(8);第一反應罐(6)下部出口管線上裝有閥門(17)和泵(18),泵(18)的出口與廢液儲存池(20)之間有管線連接;在第一反應罐(6)中下部有出料口,出料口有管線連接第二反應罐(7)的入料口;在第一反應罐(6)與第二反應罐(7)之間的管線上通過三通和管線連接加藥罐B(16)的出口;第二反應罐(7)下部也連接蒸氣管道(19),第二反應罐(7)內(nèi)底部有過濾廢液的過濾板B(9);第二反應罐(7)下部出口管線上裝有閥門和泵,第一反應罐(6)和第二反應罐(7)下部出口管線泵的出口通過管線與廢液儲存池(20)進口連接,廢液儲存池出液口連接有泵和管線,管線與補水系統(tǒng)(4)、加藥罐A(15)和加藥罐B(16)的進液口聯(lián)通;在第二反應罐(7)中下部有出料口,出料口有管線連接貯碳槽(10)的入口;在貯碳槽(10)中裝有攪拌器(11),貯碳槽(10)下部出口管線與離心機(12)進口管線連接;離心機(12)的出水口連接有泵和管線,管線與補水系統(tǒng)(4)、加藥罐A(15)和加藥罐B(16)的進液口聯(lián)通;離心機(12)的出料口與回轉干燥機(13)進料口連接;回轉干燥機(13)的出料口與干式球磨機(14)進料口連接。
說明書
一種含油污泥熱解殘渣中碳分離回收的方法
技術領域
本發(fā)明涉及采油廢水與油泥污染處理技術領域,特別涉及一種含油污泥熱解殘渣中碳分離回收的方法。
背景技術
含油污泥熱化學處理和資源化新方法探索,代表著固體廢物處理領域的先進方向和發(fā)展趨勢。含油污泥熱解殘渣為油田含油污泥通過高溫熱解法處理后產(chǎn)生的廢物殘渣,通常稱為熱解殘渣,是本發(fā)明稱的熱解殘渣。熱解殘渣中碳含量達40%左右,有較高的分離回收價值。與含油污泥的熱解是針對其中的有機成分相比,熱解殘渣的資源化利用主要是針對其中以焦炭和灰渣的形式殘留下來的無機成分,這些殘渣若處理不當,就會造成二次污染。本技術以含油污泥熱解殘渣為對象,按照“無害化、減量化、資源化”的原則,針對熱解殘渣的自身特性,從資源利用模式上進行新的探索,研究含油污泥熱解殘渣中碳的分離回收技術,同時通過對回收的殘?zhí)寂c商品炭黑、滲碳劑、活性碳的結構與特性對比研究,探索回收碳在冶金工業(yè)、二硫化碳生產(chǎn)、炭磚生產(chǎn)、輪胎、橡膠、油墨生產(chǎn)中作為添加劑以及作為吸附劑、脫色劑、催化劑載體等方面應用的可能性,為其產(chǎn)業(yè)化應用和污染控制技術提供必要的理論基礎和可靠的科學依據(jù)。含油污泥熱解殘渣中碳分離回收技術研究,符合國家提出的建設資源節(jié)約型、環(huán)境友好型社會的理念,具有重要的環(huán)境效益、經(jīng)濟效益、社會效益和一定的學術意義。
目前,由于熱解技術并未廣泛使用,所以國內(nèi)外對于含油污泥熱解殘渣資源化利用的研究也相對較少,主要還側重于熱解過程研究和熱解中產(chǎn)生的氣、固、液產(chǎn)物的分析上,而對于固體殘渣,只提及有得到炭黑一類產(chǎn)品的可能性。中國專利公開號:101113067A,公開了一種含油污泥的資源化處理方法:將含油污泥送入密閉的干餾裂解爐內(nèi)進行熱解處理,熱解處理在200~600℃條件下反應1~5小時,回收油、氣、水;在含有無機鋁鹽或鐵鹽絮凝藥劑的污泥的熱解殘渣中按鋁鹽或鐵鹽的化學當量的1∶1~5加入硫酸或鹽酸進行酸溶處理,產(chǎn)品回用到污水處理系統(tǒng)作絮凝藥劑,或回用作污泥濃縮藥劑;以粘土礦物為主的熱解殘渣直接用作廢水與油品脫色吸附材料或用作潤滑油補充精制的吸附劑;該方法在油田集輸處理系統(tǒng)中實施,實現(xiàn)集輸處理過程污泥“零排放”。從檢索的國內(nèi)外相關資料來看,未見報道含油污泥熱解殘渣中碳分離回收的藥劑配方及殘渣中碳回收的工藝方法。
發(fā)明內(nèi)容
本發(fā)明的目的是:提供一種含油污泥熱解殘渣中碳分離回收的方法,將含油污泥熱解殘渣中碳分離回收,碳純度達95%以上。通過物理化學方法,去除熱解殘渣中除碳以外的其他物質。
本發(fā)明采用的技術方案是:含油污泥熱解殘渣中碳分離回收方法使用的裝置,使用的裝置是由攪拌機、活化反應爐、螺旋輸送機、反應罐、加藥罐、蒸氣管道、過濾板、貯碳槽、離心機、干燥機、球磨機和廢液儲存池組成。攪拌機出口與活化反應爐入口連接,活化反應爐出口安裝有螺旋輸送機;螺旋輸送機的出口連接回收桶的進料口,通過螺旋輸送機將活化后殘渣輸送到回收桶中。
回收桶與補水系統(tǒng)連接,回收桶下部出料口有管線與第一反應罐上部進料口連接,利用液位差并通過補水系統(tǒng)的進水將回收桶內(nèi)殘渣沖入反應桶中。在回收桶和第一反應罐之間的管線上通過三通和管線連接加藥罐A的出口。第一反應罐下部連接有蒸氣管道,能為第一反應罐內(nèi)提供過熱蒸汽。第一反應罐內(nèi)底部有過濾廢液的過濾板A;第一反應罐下部出口管線上裝有閥門和泵,泵的出口通過管線與廢液儲存池進口連接,廢液儲存池出液口連接有泵和管線,管線與補水系統(tǒng)、加藥罐A和加藥罐B的進液口聯(lián)通。在第一反應罐中下部有出料口,出料口有管線連接第二反應罐的入料口;在第一反應罐與第二反應罐之間的管線上通過三通和管線連接加藥罐B的出口。第二反應罐下部也連接蒸氣管道,第二反應罐內(nèi)底部有過濾廢液的過濾板B;第二反應罐下部出口管線上裝有閥門和泵,泵的出口通過管線與廢液儲存池進口連接,廢液儲存池出液口連接有泵和管線,管線與補水系統(tǒng)、加藥罐A和加藥罐B的進液口聯(lián)通。在第二反應罐中下部有出料口,出料口有管線連接貯碳槽的入口,能使物料從第二反應罐被水沖入貯碳槽中。在貯碳槽中裝有攪拌器,貯碳槽下部出口管線與離心機進口管線連接。離心機的出水口連接有泵和管線,管線與補水系統(tǒng)、加藥罐A和加藥罐B的進液口聯(lián)通。離心機脫出的液體能返回補水系統(tǒng)或加藥罐A或加藥罐循環(huán)使用。離心機的出料口與回轉干燥機進料口連接,濕碳從離心機進入回轉干燥機;剞D干燥機的出料口與干式球磨機進料口連接。
含油污泥熱解殘渣中碳分離回收的方法:
A、熱解殘渣和活化劑同時加入攪拌機攪拌均勻,熱解殘渣與活化劑的質量比為1∶2~1∶4;活化劑是氯化物溶液和硫化物溶液的混合液,其中氯化物含有銨、鈉、鐵、鋁、鋅、硼、鎂、錳或鈣中的一種陽離子,優(yōu)選氯化鋅;硫化物含有鈉或鉀中的一種陽離子,優(yōu)選硫化鉀,氯化物溶液與硫化物溶液的體積比為1∶0.3~1∶0.45,氯化物溶液與硫化物溶液的濃度均為3mol/L。
B、然后將熱解殘渣和活化劑送入活化反應爐進行活化處理,升溫速度:5~10℃/min,活化處理的溫度在400~900℃,活化處理的時間為1~4小時,在活化反應爐內(nèi)形成活化后熱解殘渣。
C、將活化后熱解殘渣通過螺旋輸送機輸送入回收桶中,利用回收桶與第一反應罐的高度差,并利用補水系統(tǒng)的水將活化后熱解殘渣沖入第一反應罐中。
D、同時利用第一加藥罐往第一反應罐內(nèi)加入試液A,活化后熱解殘渣與試液A質量比為1∶2~1∶15;試液A是硫酸溶液、鹽酸溶液、磷酸溶液和氫氟酸溶液中一種或兩種的混合物,濃度為1~8mol/L。
E、通過蒸氣管道往第一反應罐內(nèi)通入120℃蒸汽20~60分鐘;開啟第一反應罐底部過濾板A放出第一反應罐內(nèi)的廢液,用水漂洗殘渣3~8次,用泵將廢液和漂洗廢水打入廢液儲存池儲存,儲存池上清液返回補水系統(tǒng)或第一加藥罐或第二加藥罐再使用。
F、將第一反應罐內(nèi)經(jīng)試液A處理工序后熱解殘渣用水沖入第二反應罐內(nèi);同時利用第二加藥罐向第二反應罐內(nèi)加入試液B,經(jīng)試液A處理工序后熱解殘渣與試液B的質量比為1∶3~1∶12;試液B為氫氧化鈉溶液、氫氧化鉀溶液中的一種,試液B重量百分比濃度為1%~15%;通入120℃蒸汽20~40分鐘;開啟第二反應罐底部過濾板B放出第二反應罐內(nèi)的廢液,用水漂洗殘渣3~8次至溶液呈中性,用泵將廢液和漂洗廢水打入廢液儲存池儲存,儲存池上清液返回補水系統(tǒng)或第一加藥罐或第二加藥罐再使用。
G、將第二反應罐內(nèi)經(jīng)試液B處理工序后熱解殘渣從第二反應罐沖入貯碳槽中;然后開動貯碳槽內(nèi)的攪拌器,使漂洗碳與水混合。
H、將漂洗碳和水通過貯碳槽底部閥門進入離心機進行脫水,液體通過泵返回補水系統(tǒng)或第一加藥罐或第二加藥罐循環(huán)使用。脫水后的濕碳輸送入回轉干燥機進行干燥處理。干燥后的碳送入干式球磨機粉碎到120~200目。
含油污泥熱解殘渣中碳分離回收的方法,是通過一系列物理和化學方法,去除熱解殘渣中除碳以外的其他物質,經(jīng)處理后的殘渣中碳純度達到95%以上,取得了很好的回收碳的效果。本技術回收的碳通過電鏡掃描、能譜分析及碘吸附值測定,在微觀結構和特性上與商品碳黑、活性碳有許多相似之處,回收的碳能作為碳磚、輪胎、橡膠、油墨、電極生產(chǎn)中的添加劑使用,也有將其開發(fā)作為吸附劑、脫色劑、催化劑載體等方面應用的可行性。為后續(xù)資源化利用創(chuàng)造條件。
本發(fā)明的有益效果:本發(fā)明含油污泥熱解殘渣中碳分離回收的方法,
1.分離回收效果好:將自主開發(fā)的回收藥劑配方按一定順序加入熱解殘渣中,經(jīng)“活化劑活化、熱解活化、精洗、分離和干燥”工藝處理后,回收的碳純度達95%以上,在微觀結構和特性上接近商品級炭黑、活性碳。
2.占地。汉臀勰酂峤鈿堅刑挤蛛x回收裝置占地面積較小,在石油企業(yè)油氣田環(huán)境保護中適用性強。
3.結構簡單,操作方便:本發(fā)明工藝裝置結構簡單,加工安裝方便,操作可實現(xiàn)自動化。
4.經(jīng)濟可行:本發(fā)明具有無二次污染,能回收碳資源,能耗低,運行成本低等特點,在實現(xiàn)含油污泥熱解殘渣無害化處理的同時,也為熱解殘渣中碳的進一步資源化利用打下了很好的基礎。
5.回收得到的碳經(jīng)過電鏡掃描、能譜分析及碘吸附值測定,在微觀結構和特性上與商品炭黑、活性碳有許多相似之處,回收的碳能作為炭磚、輪胎、橡膠、油墨、電極生產(chǎn)中的添加劑使用,也有將其開發(fā)作為吸附劑、脫色劑、催化劑載體等方面應用的可行性。為后續(xù)資源化利用創(chuàng)造了條件。