申請(qǐng)日2017.11.07
公開(公告)日2018.01.23
IPC分類號(hào)C25C1/10; C25C7/02; C22B7/00; C22B34/22
摘要
本發(fā)明涉及沉釩廢水中釩和錳的回收方法,屬于冶金化工技術(shù)領(lǐng)域。本發(fā)明所要解決的技術(shù)問題是提供沉釩廢水中釩和錳的回收方法,該方法包括如下步驟:將沉釩廢水置于電鍍槽中,通入直流電,將+5價(jià)V還原為+4價(jià)V,調(diào)節(jié)pH至6.0~7.0,固液分離,即得含釩渣;所述沉釩廢水中含有+2價(jià)Mn;厥这C以后,向固液分離得到的液體中添加二氧化硒,電解,即得金屬錳。本發(fā)明方法具有以下優(yōu)點(diǎn):(1)將沉釩廢水中的錳資源以高純度金屬錳的方式回收,其中的釩則形成含釩渣,可返回主工藝焙燒中;(2)回收釩、錳資源后的溶液可用于鈣化熟料酸性浸出中,實(shí)現(xiàn)了廢水的循環(huán)利用。
摘要附圖
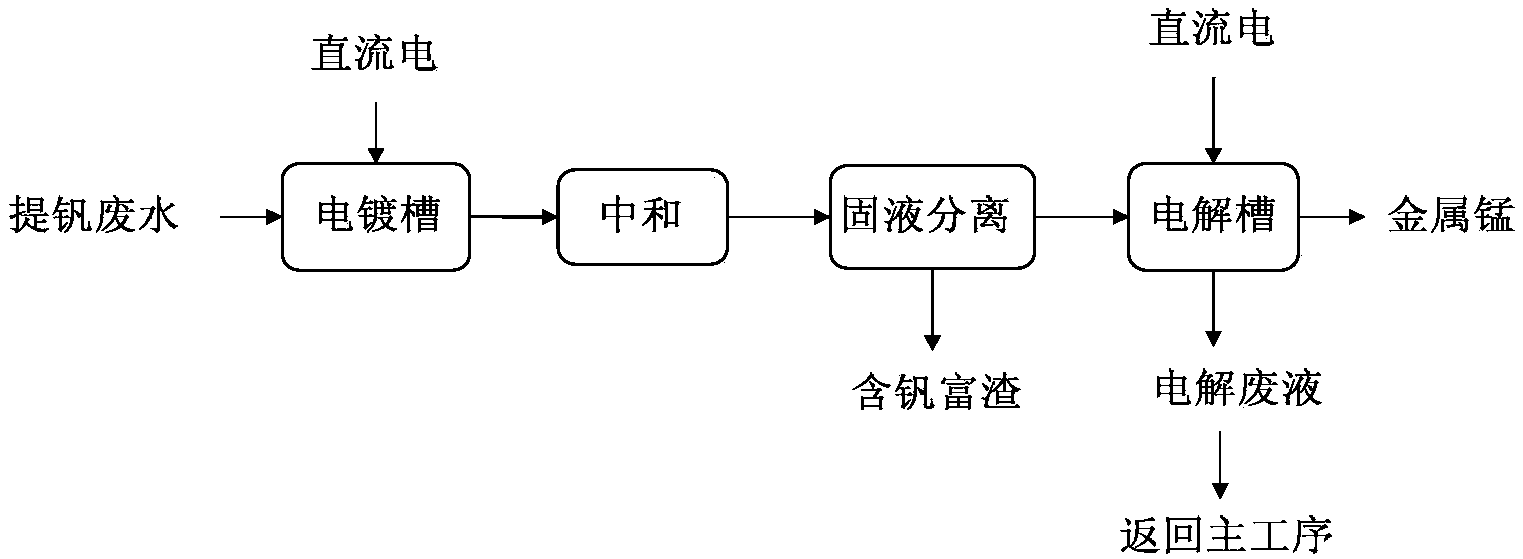
權(quán)利要求書
1.沉釩廢水中釩的回收方法,其特征是:包括如下步驟:將沉釩廢水置于電鍍槽中,通入直流電,將+5價(jià)V還原為+4價(jià)V,調(diào)節(jié)pH至6.0~7.0,固液分離,即得含釩渣;所述沉釩廢水中含有+2價(jià)Mn。
2.如權(quán)利要求1所述的回收方法,其特征是:調(diào)節(jié)pH至7.0。
3.如權(quán)利要求1所述的回收方法,其特征是:所述電鍍槽的陽極材料為鐵、碳或鉛銀合金。
4.如權(quán)利要求1所述的回收方法,其特征是:所述直流電的電壓為2~4V;優(yōu)選為4V。
5.如權(quán)利要求1所述的回收方法,其特征是:所述直流電的通電時(shí)間為10~30min;優(yōu)選為30min。
6.如權(quán)利要求1所述的回收方法,其特征是:采用氨水或氧化鈣調(diào)節(jié)pH。
7.如權(quán)利要求1所述的回收方法,其特征是:所述沉釩廢水滿足以下至少一項(xiàng):
所述沉釩廢水是生產(chǎn)氧化釩產(chǎn)生的;
所述沉釩廢水是由釩渣鈉化焙燒—水浸提釩工藝或釩渣鈣化焙燒—酸浸提釩工藝產(chǎn)生的。
8.沉釩廢水中錳的回收方法,其特征是:包括如下步驟:根據(jù)權(quán)利要求1~7任意一項(xiàng)所述方法回收釩;向固液分離得到的液體中添加二氧化硒,電解,即得錳單質(zhì)。
9.如權(quán)利要求8所述的回收方法,其特征是:所述二氧化硒的加入量為0.01~0.02g/L。
10.如權(quán)利要求8所述的回收方法,其特征是:所述電解條件滿足以下至少一項(xiàng):
電流密度為180~280A/m2;
電解溫度為20~30℃;
陽極材料為鉛銀合金;
陰極材料為不銹鋼。
說明書
沉釩廢水中釩和錳的回收方法
技術(shù)領(lǐng)域
本發(fā)明涉及沉釩廢水中釩和錳的回收方法,屬于冶金化工技術(shù)領(lǐng)域。
背景技術(shù)
在氧化釩生產(chǎn)中,轉(zhuǎn)爐釩渣經(jīng)破碎、球磨后配入一定量的鈉鹽或鈣鹽,進(jìn)入回轉(zhuǎn)窯或多膛焙燒爐進(jìn)行焙燒,將釩渣中的低價(jià)釩氧化為可溶于水的五價(jià)釩,經(jīng)浸出、沉淀、干燥、還原等工序得到氧化釩產(chǎn)品。其中,在浸出工序,原料釩渣中的錳會(huì)隨著釩共同進(jìn)入到溶液中,其中的釩濃度約為25~35g/L、錳濃度約為10~20g/L。在沉淀工序,99%的釩以多釩酸銨沉淀形式富集,而99%以上的錳及約1%的釩則留在沉淀廢水中。由于錳濃度較高,沉釩廢水的循環(huán)使用比較困難。目前有報(bào)道采用中和法將廢水中錳離子濃度降低到5g/L以下,以保證廢水的循環(huán)利用,實(shí)現(xiàn)廢水零排放。該水處理法設(shè)備與工藝成熟、操作方便簡單,但存在廢水處理渣量大、釩和錳資源未得到有效回收等問題。
針對(duì)鈣化焙燒工藝產(chǎn)生的沉釩廢水,專利CN102838233A采用石灰乳調(diào)節(jié)酸性沉釩廢水至堿性,然后進(jìn)行固液分離,得到堿性溶液和石膏渣;向堿性溶液中加入脫鈣劑進(jìn)行脫鈣,然后進(jìn)行固液分離,得到上層清液和脫鈣渣;用硫酸將上層清液的pH值調(diào)節(jié)至3~7后返回浸出工序進(jìn)行循環(huán)利用。該方法實(shí)現(xiàn)了廢水的循環(huán)利用,能夠有效控制了返回浸出工序的溶液中的鈣離子濃度,避免硫酸鈣沉淀的形成,但廢水中大量的錳資源沒有得到有效回收,礦石利用率低。
針對(duì)鈉化焙燒工藝產(chǎn)生的沉釩廢水:專利CN102051486A將沉釩廢水作為含釩熟料的浸取劑,利用其所含銨根離子和磷酸根離子與鎂離子形成絡(luò)合沉淀物,再加入除磷劑進(jìn)行深度除磷,從而制取低磷釩液,實(shí)現(xiàn)了沉釩廢水的再利用;專利CN101812593A將酸性廢水用于提釩尾渣的清洗后再進(jìn)行還原、中和、蒸發(fā)濃縮,以減少廢水處理工序中中和所用的堿量。
然而,目前尚未見對(duì)沉釩廢水中的釩和錳資源進(jìn)行回收利用的報(bào)道。
發(fā)明內(nèi)容
本發(fā)明的目的在于提供沉釩廢水中釩和錳的回收方法。
本發(fā)明提供了沉釩廢水中釩的回收方法,包括如下步驟:將沉釩廢水置于電鍍槽中,通入直流電,將+5價(jià)V還原為+4價(jià)V,調(diào)節(jié)pH至6.0~7.0,固液分離,即得含釩渣;所述沉釩廢水中含有+2價(jià)Mn。
進(jìn)一步地,調(diào)節(jié)pH至7.0。
進(jìn)一步地,調(diào)節(jié)pH時(shí)攪拌10~30min。
進(jìn)一步地,所述電鍍槽的陽極材料為鐵、碳或鉛銀合金。
進(jìn)一步地,所述電鍍槽的陰極選用導(dǎo)電材料即可,如不銹鋼。
進(jìn)一步地,所述直流電的電壓為2~4V;優(yōu)選為4V。
進(jìn)一步地,所述直流電的通電時(shí)間為10~30min;優(yōu)選為30min。
進(jìn)一步地,采用氨水或氧化鈣調(diào)節(jié)pH。
進(jìn)一步地,所述沉釩廢水是生產(chǎn)氧化釩產(chǎn)生的。
進(jìn)一步地,所述沉釩廢水是由釩渣鈉化焙燒—水浸提釩工藝或釩渣鈣化焙燒—酸浸提釩工藝產(chǎn)生的。
本發(fā)明提供了沉釩廢水中錳的回收方法,包括如下步驟:根據(jù)所述方法回收釩;向固液分離得到的液體中添加二氧化硒,電解,即得錳單質(zhì)。
進(jìn)一步地,所述二氧化硒的加入量為0.01~0.02g/L。
進(jìn)一步地,所述電解的電流密度為180~280A/m2。
進(jìn)一步地,所述電解溫度為20~30℃。
進(jìn)一步地,陽極材料為鉛銀合金。
進(jìn)一步地,陰極材料為不銹鋼。
本發(fā)明提供了一種有效回收沉釩廢水中釩、錳資源的途徑,具有以下優(yōu)點(diǎn):
(1)將沉釩廢水中的錳資源以高純度單質(zhì)錳的形式回收(純度達(dá)到99%以上),沉釩廢水中的釩則形成含釩渣,可返回主工藝焙燒中,同樣實(shí)現(xiàn)了回收利用;
(2)回收釩、錳資源后的溶液可用于鈣化熟料酸性浸出中,實(shí)現(xiàn)了廢水的循環(huán)利用。