申請日2010.07.27
公開(公告)日2011.01.05
IPC分類號C02F1/72; C02F1/30
摘要
本發(fā)明提供了一種微波氧化廢水處理系統(tǒng)及廢水處理方法,可以解決現(xiàn)有技術(shù)存在的水處理效率偏低、常壓下的微波氧化易使水體汽化蒸發(fā)造成能量浪費的問題。技術(shù)方案是:一種微波氧化廢水處理系統(tǒng),包括微波發(fā)生器、微波催化氧化裝置、加壓泵、加藥裝置、汽水分離器。同時還提供了采用上述系統(tǒng)的廢水處理方法。本發(fā)明在相對高溫高壓條件下進(jìn)行處理,提高了處理效率,系統(tǒng)結(jié)構(gòu)緊湊,占地面積小,自動化程度高,操作簡便。
摘要附圖
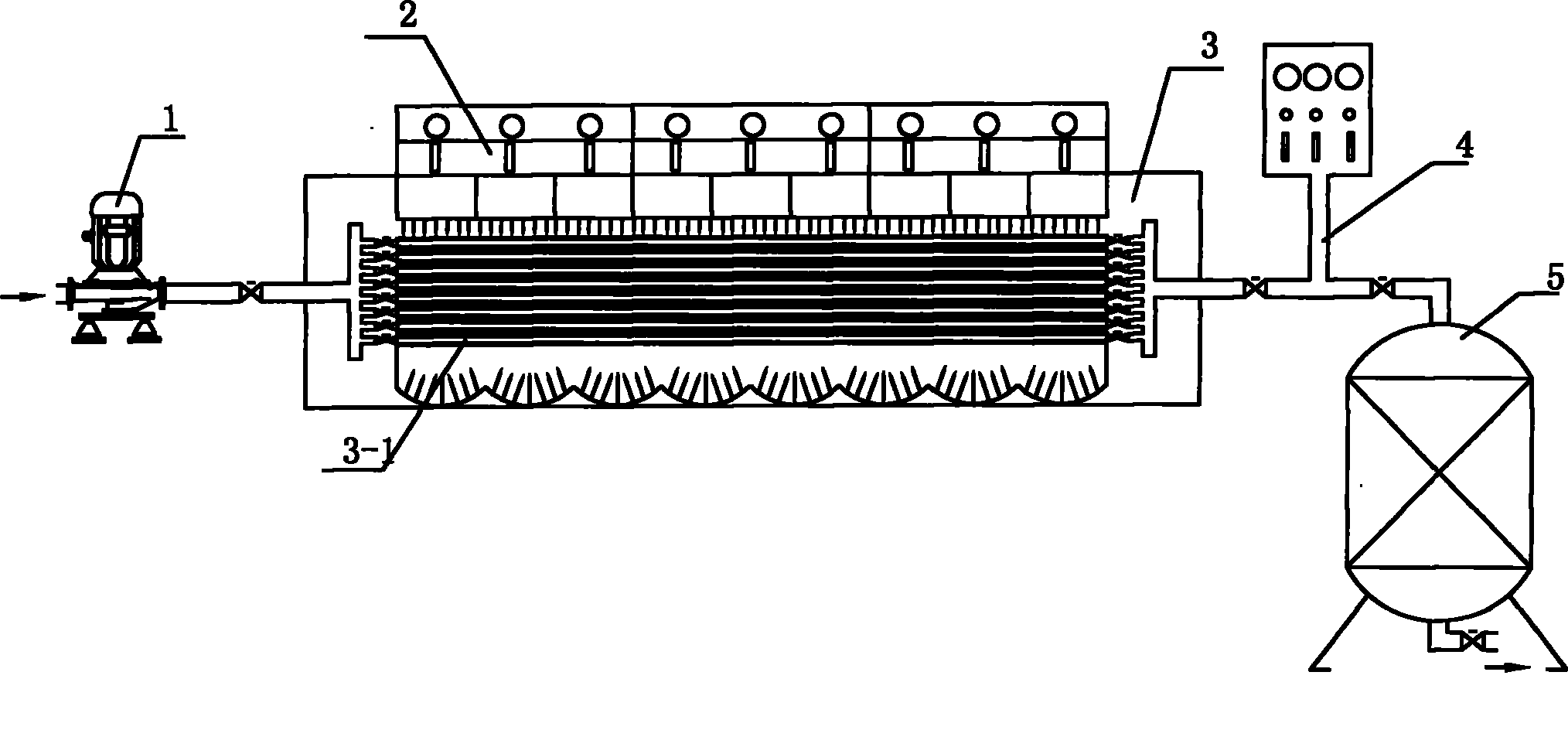
權(quán)利要求書
1.一種微波氧化廢水處理系統(tǒng),包括可調(diào)微波發(fā)生器、微波催化氧化裝置,其特征在于:還包括加壓泵、加藥裝置、汽水分離器,廢水經(jīng)加壓泵加壓后進(jìn)入微波催化氧化裝置,然后進(jìn)入汽水分離器內(nèi)冷卻后排出。
2.根據(jù)權(quán)利要求1所述的微波氧化廢水處理系統(tǒng),其特征在于:所述微波催化氧化裝置內(nèi)設(shè)有密閉的管道,所述管道由PVC管構(gòu)成。
3.根據(jù)權(quán)利要求2所述的微波氧化廢水處理系統(tǒng),其特征在于:所述PVC管內(nèi)裝有鈦、鐵、錳三元催化劑。
4.根據(jù)權(quán)利要求3所述的微波氧化廢水處理系統(tǒng),其特征在于:所述PVC管設(shè)有13根,在所述微波催化氧化裝置內(nèi)均勻間隔環(huán)狀排列。
5.根據(jù)權(quán)利要求1或4所述的微波氧化廢水處理系統(tǒng),其特征在于:所述汽水分離器上部設(shè)有排氣閥。
6.一種微波氧化廢水處理方法,其特征在于包括如下步驟:
(1)待處理廢水與氧化劑混合后進(jìn)入加壓泵進(jìn)行加壓;加壓到4-16Kg/cm2;
(2)被加壓后的廢水進(jìn)入微波氧化裝置,微波發(fā)生器發(fā)出微波輻照PVC管,廢水在微波和催化劑的作用下迅速降解其中有機污染物,廢水在PVC管內(nèi)停留30-120S,反應(yīng)溫度110-200℃,反應(yīng)壓力0.3-1.6MPa,微波反應(yīng)器功率200-1000W,完成催化氧化反應(yīng);
(3)廢水自微波催化氧化裝置進(jìn)入汽水分離器,在汽水分離器內(nèi)冷卻,同時壓力降低;
(4)當(dāng)壓力降到常壓時,廢水中的低沸點有機物迅速揮發(fā)通過排氣閥排出。
7.根據(jù)權(quán)利要求5所述的廢水處理方法,其特征在于:所述氧化劑為氧氣或空氣。
8.根據(jù)權(quán)利要求5所述的廢水處理方法,其特征在于:所述廢水為高濃度生物法難降解有毒有害有機廢水,其COD值為3000-200000mg/L。
9.根據(jù)權(quán)利要求5所述的廢水處理方法,其特征在于:經(jīng)過所述廢水處理方法處理后的廢水COD去除率為60-75%。
說明書
微波氧化廢水處理系統(tǒng)及廢水處理方法
技術(shù)領(lǐng)域
本發(fā)明屬于廢水處理領(lǐng)域,具體來說,設(shè)計一種微波氧化廢水處理系統(tǒng)及廢水處理方法,所述系統(tǒng)用于處理高濃度、生物法難降解有機廢水。
背景技術(shù)
高濃度難降解有機廢水是指難降解、可生化性差,其BOD5/COD值很小,通常小于0.2,而COD高或色度高的有機廢水。水量不是很大,但污染負(fù)荷很大,采用傳統(tǒng)的生物法難以達(dá)到預(yù)期的降解效果。其主要來源是造紙、染料、制藥、煉油、有機合成、農(nóng)藥生產(chǎn)等行業(yè)生產(chǎn)廢水。這類廢水一旦進(jìn)入到環(huán)境系統(tǒng)中會造成及其嚴(yán)重的后果,往往引起環(huán)境系統(tǒng)的不可逆損害。
已有的催化濕式氧化法通常是在高溫(200-350℃)、高壓(2-20MPa)下,以CIO2作為氧化劑,在催化劑作用下,氧化去除水中有機物,最終達(dá)到礦化的目的。在國外這種技術(shù)發(fā)展較快,20世紀(jì)70年代開始,日本相繼成立了濕式催化裝置處理各種有機廢水,如日本三菱石油化學(xué)公司處理乙烯生產(chǎn)廢水洗滌液,其操作條件:200℃,3.45MPa,停留60分鐘,處理量為120m3/d,進(jìn)水COD為7.5-15g/L,COD去除率為67%-80%;日本川崎朝日化學(xué)公司處理丙烯氰生產(chǎn)廢水,其操作條件:250℃.7MPa,停留90分鐘,處理量790m3/d,進(jìn)水COD為37-46g/L,出水COD為14.8-16.1g/L,COD去除率為60%-65%.從80年代到90年代有較多的研究報道,目前該技術(shù)仍在研究深化中。中國科學(xué)院大連化學(xué)物理研究所的杜鴻章等與冶金部鞍山焦化耐火材料設(shè)計研究院的尹承龍等,在1997年發(fā)表了關(guān)于催化濕式氧化法處理難降解高濃度有機廢水的研究結(jié)果。其詳細(xì)情況見《水處理技術(shù)》,杜鴻章,1997年6月發(fā)表的“難降解高濃度有機廢水濕式催化凈化技術(shù)”文章。該項研究中主要反應(yīng)器是由TA3型鈦鋼加工成的,其設(shè)計壓力為12MPa,使用溫度小于360℃.反應(yīng)器內(nèi)徑16mm,長500mm。工藝過程中使用的設(shè)備有空氣瓶、壓力表、前壓力控制器、氣體調(diào)節(jié)閥、質(zhì)量流量計、水計量管等。處理廢水的步驟:氧化劑氣體(空氣)來自鋼瓶,經(jīng)前壓力控制器調(diào)至所需壓力,在經(jīng)質(zhì)量流量計后與高微量進(jìn)料泵輸來的原水混合預(yù)熱后,由反應(yīng)器底部進(jìn)入反應(yīng)器,反應(yīng)器內(nèi)上、下添裝瓷粒.中間裝催化劑,床層高約7.5cm,反應(yīng)后的物料由反應(yīng)器上端出來,依次經(jīng)冷凝器和分離器冷卻、分離,液體進(jìn)入儲水罐時取樣分析,氣體經(jīng)后壓力調(diào)節(jié)器及尾氣流量計放空。反應(yīng)的最佳工藝條件為270℃.9MPa,空氣量為6.2L/h,進(jìn)料空速為2.0h-1。該工藝的不足之處:(1)反應(yīng)必須在270℃、9MPa條件下進(jìn)行方可得到滿意結(jié)果;(2)自制催化劑的價格昂貴;(3)廢水與反應(yīng)器直接接觸,容易對反應(yīng)器的材質(zhì)腐蝕。
微波作為一種電磁波,被譽為20世紀(jì)最偉大的發(fā)明之一,與傳導(dǎo)加熱相比,微波具有加熱速度快、加熱效率高、加熱均勻、溫度由物體內(nèi)部向外部擴散等特點。已經(jīng)有大量研究表明,對于化學(xué)反應(yīng),微波除具有熱效應(yīng)之外,還具有非熱效應(yīng).微波每秒上億次交變的電場與磁場將對大分子有機物的鏈狀結(jié)構(gòu)進(jìn)行強烈的振蕩,使其破壞與斷裂、形成小分子結(jié)構(gòu),再進(jìn)行催化氧化,最終分解為CO2和H2O.近些年來微波已被廣泛的應(yīng)用到濕式催化氧化領(lǐng)域中,如大連理工大學(xué)發(fā)明的“微波催化氧化處理難解有機廢水的工藝與裝置”,專利號:02118708.8。該項研究中的工藝包括:格柵去雜、絮凝沉降、催化氧化與蒸汽冷凝。催化氧化是在微波反應(yīng)器中進(jìn)行,最佳工藝條件為:氧化劑質(zhì)量與廢水COD質(zhì)量的比例為1.0-20%,溫度低于100℃,停留時間4-17min,廢水COD去除率在95%左右。該工藝的不足之處在于:(1)由于廢水在常壓下進(jìn)行微波輻射,極易使廢水的溫度達(dá)到沸點,由于汽化的原因會造成大量的能量浪費;(2)反應(yīng)溫度只能達(dá)到100℃,從化學(xué)反應(yīng)動力學(xué)來看,對化學(xué)反應(yīng)速度有所限制。
發(fā)明內(nèi)容
本發(fā)明提供了一種微波氧化廢水處理系統(tǒng)及廢水處理方法,可以解決現(xiàn)有技術(shù)存在的水處理效率偏低、常壓下的微波氧化易使水體汽化蒸發(fā)造成能量浪費的問題。
為解決上述技術(shù)問題,本發(fā)明采用以下技術(shù)方案予以實現(xiàn):
一種微波催化氧化廢水處理系統(tǒng),包括微波發(fā)生器、微波催化氧化裝置,還包括加壓泵、加藥裝置、汽水分離器,廢水經(jīng)加壓泵加壓后進(jìn)入微波催化氧化裝置,然后進(jìn)入汽水分離器內(nèi)減壓氧化后排出。
本發(fā)明的基本構(gòu)思是利用微波電磁能傳播技術(shù)與汽水分離器相結(jié)合的一種新型水處理系統(tǒng),在反應(yīng)體系施加一定的壓力,既提高了反應(yīng)溫度,又保證了反應(yīng)在液相中進(jìn)行,而且充分體現(xiàn)了微波“非熱效應(yīng)”的優(yōu)勢--降解速度快、降解效率高、能量利用率高、設(shè)備不易被腐蝕。利用微波的熱效應(yīng)和非熱效應(yīng)使有機污染物在催化劑和氧化劑存在的條件下進(jìn)行微波氧化反應(yīng)。而后在汽水分離器內(nèi)減壓氧化,使得有機物極易被汽化,處理比較容易。
進(jìn)一步地,為了防止反應(yīng)器被高濃度有機廢水腐蝕,特別是壓力容器易造成安全隱患,所述微波催化氧化裝置內(nèi)設(shè)有密閉的管道,所述管道由PVC管構(gòu)成,通過微波輻照所述管道而降解廢水。
再進(jìn)一步地,為了降低成本,所述聚四氟乙烯管內(nèi)裝有鈦、鐵、錳三元催化劑,解決了現(xiàn)有技術(shù)采用的催化劑價格昂貴,在使用過程中易中毒或流失,造成水處理成本偏高,企業(yè)難以承受的問題。
更進(jìn)一步地,所述PVC管設(shè)有13根,在所述微波催化氧化裝置內(nèi)均勻間隔環(huán)狀排列。
為了方便排出汽化的有機物,所述汽水分離器上部設(shè)有排氣閥,低沸點有機物通過排氣閥揮發(fā)排出。
一種微波氧化廢水處理方法,包括如下步驟:
(1)待處理廢水與氧化劑混合后進(jìn)入加壓泵進(jìn)行加壓;加壓到4-16Kg/cm2;
(2)被加壓后的廢水進(jìn)入微波催化氧化裝置,微波發(fā)生器發(fā)出微波輻照PVC管,廢水在微波的作用下迅速降解其中有機污染物,廢水在PVC管內(nèi)停留30-120S,反應(yīng)溫度110-200℃,反應(yīng)壓力0.3-1.6MPa,微波反應(yīng)器功率200-1000W,完成催化氧化反應(yīng),廢水的COD降低50-65%;
(3)廢水自微波催化氧化裝置進(jìn)入汽水分離器,在汽水分離器內(nèi)氧化劑繼續(xù)與廢水中的有機物反應(yīng),同時壓力降低;
(4)當(dāng)壓力降到常壓時,廢水中的低沸點有機物迅速揮發(fā)通過排氣閥排出。
根據(jù)廢水COD濃度的不同,相應(yīng)采取不同的工藝參數(shù),如反應(yīng)溫度、反應(yīng)壓力、微波反應(yīng)器功率,一般是隨其水COD濃度越大,其工藝參數(shù)的選擇就越接近參數(shù)范圍的上限值,反之選取下限值。
針對現(xiàn)有濕式催化氧化技術(shù),必須在200-350℃高溫,2-20MPa高壓下反應(yīng),反應(yīng)條件比較苛刻,對設(shè)備的要求較高,建造成本也較高的問題,通過加壓泵對系統(tǒng)加壓,提高了反應(yīng)溫度,又保證了反應(yīng)在液相中進(jìn)行,而且充分體現(xiàn)了微波“非熱效應(yīng)”的優(yōu)勢--降解速度快、降解效率高、能量利用率高、設(shè)備不易被腐蝕。利用微波的熱效應(yīng)和非熱效應(yīng)使有機污染物在催化劑和氧化劑存在的條件下進(jìn)行微波氧化反應(yīng)。而后在汽水分離器內(nèi)減壓氧化,使得有機物極易被汽化,處理比較容易。針對常壓下的微波輔助催化氧化易使水體汽化蒸發(fā),造成能量浪費;而且反應(yīng)溫度最高100℃,從反應(yīng)動力學(xué)角度分析,限制反應(yīng)速率的缺點,本發(fā)明都得到了解決。
進(jìn)一步地,所述氧化劑為氧氣、空氣。
進(jìn)一步地,所述微波裝置裝置吸入的氧化劑為空氣。
進(jìn)一步地,所述廢水為高濃度生物法難降解有毒有害有機廢水,其COD值為3000-200000mg/L。
進(jìn)一步地,經(jīng)過所述廢水處理方法處理后的廢水COD去除率為60-75%。
本發(fā)明的上述微波氧化處理高濃度難降解有機廢水的方法,主要包括微波輻射氧化、出水排放或回用、降解和停留時間,微波爐內(nèi)均勻間隔環(huán)狀排列13根PVC管,內(nèi)置鈦、鐵、錳三元催化劑,污水在進(jìn)入微波催化裝置前,與定量的氧化劑混合,再經(jīng)水泵加壓后進(jìn)入微波氧化裝置,在微波的作用下,可迅速氧化分解污水中的有機污染物質(zhì),反應(yīng)管內(nèi)壓力與溫度同步升高到臨界值,在反應(yīng)管內(nèi)停留30-120S后,氧化反應(yīng)完成。此裝置具有結(jié)構(gòu)緊湊,占地面積小,自動化程度高,操作簡便,效率高。
上述廢水處理系統(tǒng)進(jìn)行廢水處理時的注意事項:裝置啟動前應(yīng)全面檢查儀器、設(shè)備及管線的完好性及其連接處有無滲漏,在確保上述檢查結(jié)果合格后,方可啟動廢水處理系統(tǒng)。
與現(xiàn)有技術(shù)相比,本發(fā)明的優(yōu)點和積極效果是:
(1)利用微波輻射進(jìn)行處理,由于微波的熱效應(yīng)和非熱效應(yīng)同時起作用,所以有機物降解速度快、效率高,比現(xiàn)有的傳導(dǎo)加熱方法提高20%-40%;
(2)在相對高溫高壓條件下進(jìn)行處理,提高了處理效率;
(3)采用PVC管作為廢水接受微波輻照的管道,所以廢水并不與金屬材質(zhì)直接接觸大大降低了廢水對容器的腐蝕,使設(shè)備的使用壽命延長了2-3倍;
(4)內(nèi)置鈦、鐵、錳三元催化劑提高了處理效果;
(5)本發(fā)明系統(tǒng)結(jié)構(gòu)緊湊,占地面積小,自動化程度高,操作簡便,效率高。