申請(qǐng)日2015.09.02
公開(公告)日2015.11.18
IPC分類號(hào)C02F9/06; C02F9/14; C02F103/10; C01D3/14; C02F9/10
摘要
一種采油廢水處理及其循環(huán)利用方法,包括如下步驟:(1)將預(yù)處理后的采油廢水經(jīng)過除油工藝除去油污;(2)投加石灰乳、碳酸鈉并配合混凝劑、絮凝劑使生成碳酸鈣、碳酸鎂,經(jīng)過沉淀分離去除碳酸鈣、碳酸鎂沉淀,根除膜鈣化和防止膜堵塞;(3)過濾澄清后,經(jīng)過微濾、超濾或納濾膜過濾,去除顆粒性雜質(zhì);(4)反滲透、正滲透、電滲析、電容吸附處理得循環(huán)利用的再生水和濃縮液。本發(fā)明可有效除油、降低CODcr,降低廢水的SS、濁度等指標(biāo),脫除水中的金屬離子,降低含鹽量,實(shí)現(xiàn)采油廢水50~65%的回收率。
摘要附圖
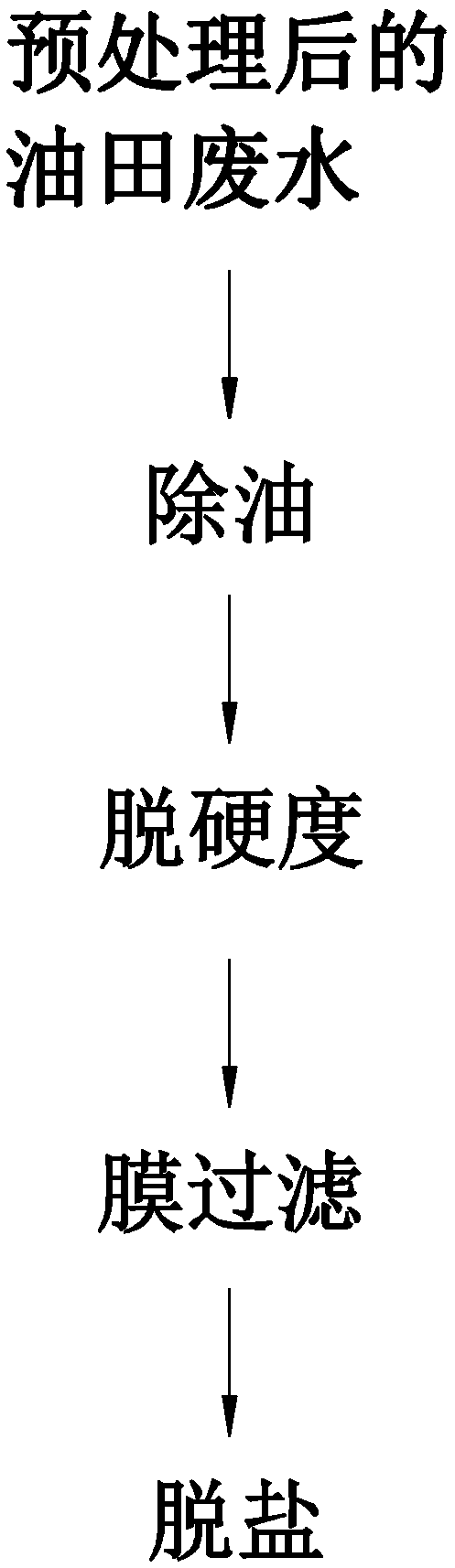
權(quán)利要求書
1.一種采油廢水處理及其循環(huán)利用方法,其特征在于,包括如下步驟:
(1)除油:將含鈣離子200~3000mg/L、鎂離子20~500mg/L、鈉離子200~8000mg/L、氯離子200~10000mg/L、含油30~300mg/L和COD為100~500mg/L的采油廢水經(jīng)過除油工藝除去油污,所述除油工藝是氣浮、活性炭吸附、粘土吸附或硅藻土吸附中的一種;
(2)脫硬度:往經(jīng)過步驟(1)除油后的采油廢水中投加石灰乳、碳酸鈉并配合混凝劑、絮凝劑使生成碳酸鈣、碳酸鎂沉淀,經(jīng)過沉淀分離去除碳酸鈣、碳酸鎂沉淀,從而將鈣、鎂離子濃度控制在小于80mg/L;
(3)膜過濾:將步驟(2)脫硬度后的采油廢水經(jīng)過過濾澄清后,經(jīng)過膜過濾處理,去除顆粒性雜質(zhì);
(4)脫鹽:將步驟(3)膜過濾所得的采油廢水經(jīng)過反滲透、正滲透、電滲析、電容吸附處理得循環(huán)利用的再生水和濃縮液。
2.如權(quán)利要求1所述的一種采油廢水處理及其循環(huán)利用方法,其特征在于:所述步驟(2)脫硬度還包括一個(gè)碳酸鈣沉淀處理工序,通過這個(gè)工序?qū)⑻妓徕}加熱氧化分解成氧氣鈣。
3.如權(quán)利要求1所述的一種采油廢水處理及其循環(huán)利用方法,其特征在于:在步驟(2)的脫硬度和步驟(3)的膜過濾之間,還包括一個(gè)去除COD的步驟,該去除COD步驟是電解、電氣浮或芬頓反應(yīng)的一種,通過去除COD使廢水中的COD濃度下降到50mg/L以下。
4.如權(quán)利要求1所述的一種采油廢水處理及其循環(huán)利用方法,其特征在于:在步驟(2)的脫硬度和步驟(3)的膜過濾之間,還包括沉淀分離和過濾工序,所述沉淀分離為沉淀池沉淀、斜管沉淀或離心沉淀分離的一種;所述過濾為砂濾、多介質(zhì)過濾或纖維濾芯過濾,除去較大顆粒雜質(zhì),保證膜過濾效果。
5.如權(quán)利要求1所述的一種采油廢水處理及其循環(huán)利用方法,其特征在于:步驟(3)的膜過濾為微濾膜過濾、超濾膜過濾或MBR中的一種,所述微濾膜為有機(jī)膜、金屬膜或陶瓷膜中的一種,其孔徑介于1μm-10μm之間;所述超濾為浸沒式超濾、柱式超濾、管式超濾、卷式超濾或板式超濾中的一種,截留分子量為1000~50000MWCO,工作條件為:常溫~45℃,浸沒式超濾的工作壓力為-1~-50kPa,柱式超濾、管式超濾、卷式超濾和板式超濾的工作壓力為3~300kPa;所述MBR膜組件的膜孔徑為0.10~0.2μm,工作壓力為-1~-50kPa,工作溫度為5~45℃。
6.如權(quán)利要求1所述的一種采油廢水處理及其循環(huán)利用方法,其特征在于:步驟(3)的膜過濾為納濾膜過濾,納濾膜采用對(duì)硫酸鎂截留率為至少98%的納濾膜,納濾膜的截留分子量為200MWCO-500MWCO,進(jìn)壓為6bar-45bar,出壓為4.5bar-43.5bar,且其膜組件的結(jié)構(gòu)為卷式膜組件或管式膜組件,工作溫度為20~45℃,納濾不僅可以去除顆粒沉淀,還可以除去40~70%的鹽。
7.如權(quán)利要求1所述的一種采油廢水處理及其循環(huán)利用方法,其特征在于:步驟(4)的脫鹽為反滲透脫鹽,反滲透中的反滲透膜組件為卷式膜組件,膜材料為有機(jī)膜中醋酸纖維膜或復(fù)合膜,膜材料的截留分子量為50~200MWCO,進(jìn)壓為6.0~35.0bar,出壓為4.5~33.5bar。
8.如權(quán)利要求1所述的一種采油廢水處理及其循環(huán)利用方法,其特征在于:步驟(4)的脫鹽為正滲透,正滲透的膜組件為板框式膜組件、卷式膜組件、管式膜組件和包式膜組件中的一種。
9.如權(quán)利要求1所述的一種采油廢水處理及其循環(huán)利用方法,其特征在于:步驟(4)的脫鹽為電滲析,電滲析的工作條件是操作電壓壓力0.5~3.0㎏/㎝2,操作電壓50~250V,電流強(qiáng)度1~3A。
10.如權(quán)利要求1所述的一種采油廢水處理及其循環(huán)利用方法,其特征在于:步驟(4)的脫鹽為電容吸附,電容吸附的工作條件是直流電壓為110V~2×106V。
11.如權(quán)利要求1所述的一種采油廢水處理及其循環(huán)利用方法,其特征在于:還包括從一個(gè)濃縮液中回收鹽的步驟,所述從濃縮液中回收鹽的步驟是將濃縮液經(jīng)過多效蒸發(fā)濃縮后結(jié)晶分離得氯化鈉和蒸餾水,或者將濃縮液排入晾曬池中經(jīng)過自然蒸發(fā)或強(qiáng)制蒸發(fā)后結(jié)晶分離得氯化鈉。
說明書
一種采油廢水處理及其循環(huán)利用方法
技術(shù)領(lǐng)域
本發(fā)明屬于環(huán)境工程的水污染治理領(lǐng)域,更為具體地說是指一種采油廢水處理及其循環(huán)利用方法。
背景技術(shù)
油田采出水主要是原油在生產(chǎn)處理過程中脫出的污水。油田采出水的處理根據(jù)排放或回用不同要求有多種方式,作為蒸汽發(fā)生器或鍋爐的給水,要嚴(yán)格控制水中的鈣離子、鎂離子等易結(jié)垢的離子含量,總礦化度、水中的含油量等。利用膜分離技術(shù)對(duì)油田采出水進(jìn)行脫鹽處理,使得產(chǎn)水再生循環(huán)利用等方面的報(bào)道不少。油田采出水經(jīng)過一般的預(yù)處理去除了大部分的含油量和懸浮物之后的主要污染物指標(biāo)為:鈣離子200~3000mg/L、鎂離子20~500mg/L、鈉離子200~8000mg/L、氯離子200~10000mg/L、含油30~300mg/L和COD為100~500mg/L。鈣離子、鎂離子、碳酸氫根離子等含量仍然很高?傆捕冗^高,直接采用膜分離技術(shù)進(jìn)行脫鹽處理,容易造成膜的鈣化和污堵,膜材料的孔隙中填滿了碳酸鈣、碳酸鎂等物質(zhì),一方面使得膜的出水水質(zhì)變差,嚴(yán)重影響膜處理系統(tǒng)的穩(wěn)定運(yùn)行,另一方面膜的鈣化會(huì)使得膜材料變脆,容易斷絲,導(dǎo)致膜的使用壽命由通常的三年以上,縮短到不到壹年,減少膜的運(yùn)行壽命,頻繁更換膜組件,經(jīng)濟(jì)上不可行。
發(fā)明內(nèi)容
本發(fā)明提供一種采油廢水處理及其循環(huán)利用方法,其主要目的在于克服現(xiàn)有技術(shù)中油田采出水膜法處理過程存在膜鈣化、污堵嚴(yán)重、成本高的缺陷。
本發(fā)明采用如下技術(shù)方案:
一種采油廢水處理及其循環(huán)利用方法,包括如下步驟:
(1)除油:將含鈣離子200~3000mg/L、鎂離子20~500mg/L、鈉離子200~8000mg/L、氯離子200~10000mg/L、含油30~300mg/L和COD為100~500mg/L的采油廢水經(jīng)過除油工藝除去油污,所述的除油工藝是氣浮、活性炭吸附、粘土吸附或硅藻土吸附的一種;
(2)脫硬度:往經(jīng)過步驟(1)除油后含鈣離子200~3000mg/L、鎂離子20~500mg/L、鈉離子200~8000mg/L、氯離子200~10000mg/L和COD為30~150mg/L的采油廢水中投加石灰乳、碳酸鈉并配合混凝劑、絮凝劑使生成碳酸鈣、碳酸鎂沉淀,經(jīng)過沉淀分離去除碳酸鈣、碳酸鎂沉淀,從而將鈣鎂離子濃度控制在小于80mg/L;
(3)膜過濾:將步驟(2)脫硬度后的采油廢水經(jīng)過過濾澄清后,經(jīng)過微濾、超濾或納濾膜過濾,去除顆粒性雜質(zhì);
(4)脫鹽:將步驟(3)膜過濾所得的采油廢水經(jīng)過反滲透、正滲透、電滲析、電容吸附處理得循環(huán)利用的再生水和濃縮液。
進(jìn)一步地,步驟(2)的脫硬度還包括一個(gè)碳酸鈣沉淀處理工序,通過這個(gè)工序?qū)⑻妓徕}加熱氧化分解成氧氣鈣。
進(jìn)一步地,在步驟(2)的脫硬度和步驟(3)的膜過濾之間,還包括一個(gè)去除COD的步驟,該去除COD步驟是電解、電氣浮或芬頓反應(yīng)的一種,通過去除COD使廢水中的COD濃度下降到50mg/L以下。
進(jìn)一步地,在步驟(2)的脫硬度和步驟(3)的膜過濾之間,還包括沉淀分離和過濾工序,所述沉淀分離為沉淀池沉淀、斜管沉淀或離心沉淀分離的一種;所述過濾為砂濾、多介質(zhì)過濾或纖維濾芯過濾,除去較大顆粒雜質(zhì),保證膜過濾效果。
進(jìn)一步地,上述步驟(3)的膜過濾是微濾膜過濾、超濾膜過濾或MBR;所述微濾膜為有機(jī)膜、金屬膜或陶瓷膜中的一種,其孔徑介于1μm-10μm之間;所述超濾為浸沒式超濾、柱式超濾、管式超濾、卷式超濾或板式超濾中的一種,截留分子量為1000~50000MWCO,工作條件為:常溫~45℃,浸沒式超濾的工作壓力為-1~-50kPa,柱式超濾、管式超濾、卷式超濾和板式超濾的工作壓力為3~300kPa;所述MBR膜組件的膜孔徑為0.10~0.2μm,工作壓力為-1~-50kPa,工作溫度為5~45℃。
進(jìn)一步地,上述步驟(3)的膜過濾是納濾膜過濾,納濾膜采用對(duì)硫酸鎂截留率為至少98%的納濾膜,納濾膜的截留分子量為200MWCO-500MWCO,進(jìn)壓為6bar-45bar,出壓為4.5bar-43.5bar,且其膜組件的結(jié)構(gòu)為卷式膜組件或管式膜組件,工作溫度為20~45℃,納濾不僅可以去除顆粒沉淀,還可以除去40~70%的鹽。
進(jìn)一步地,上述步驟(4)的脫鹽為反滲透脫鹽,反滲透中的反滲透膜組件為卷式膜組件,膜材料為有機(jī)膜中醋酸纖維膜或復(fù)合膜,膜材料的截留分子量為50~200MWCO,進(jìn)壓為6.0~35.0bar,出壓為4.5~33.5bar。
進(jìn)一步地,上述步驟(4)的脫鹽為正滲透,正滲透的膜組件為板框式膜組件、卷式膜組件、管式膜組件和包式膜組件中的一種。
進(jìn)一步地,上述步驟(4)的脫鹽為電滲析,電滲析的工作條件是操作電壓壓力0.5~3.0㎏/㎝2,操作電壓50~250V,電流強(qiáng)度1~3A。
進(jìn)一步地,上述步驟(4)的脫鹽為電容吸附,電容吸附的工作條件是直流電壓為110V~2×106V。
進(jìn)一步地,上述一種采油廢水處理及其循環(huán)利用方法,還包括從一個(gè)濃縮液中回收鹽的步驟,所述從濃縮液中回收鹽的步驟是將濃縮液經(jīng)過多效蒸發(fā)濃縮后結(jié)晶分離得氯化鈉和蒸餾水,或者將濃縮液排入晾曬池中經(jīng)過自然蒸發(fā)或者強(qiáng)制蒸發(fā)后結(jié)晶分離得氯化鈉。
經(jīng)過以上工序處理后的效果如下表1:
表1采油廢水各處理工序的效果
本發(fā)明和現(xiàn)有技術(shù)相比,具有如下優(yōu)點(diǎn):
1、采油廢水中油含量較高,本發(fā)明通過氣浮可有效除油、降低CODcr,此外,還可以采用活性炭吸附、粘土吸附等方法除去少量的油。
2、采油廢水中鈣、鎂含量高,容易造成膜鈣化和污堵,在預(yù)處理過程,通過投加石灰乳、碳酸鈉并配合混凝劑、絮凝劑將鈣、鎂離子去除,并去除一部分硫酸根離子,從而將鈣、鎂離子的濃度控制在小于80mg/L,不僅解決了膜鈣化和污堵問題,而且降低了廢水滲透壓。
3、經(jīng)過化學(xué)方法處理后的廢水再經(jīng)過膜過濾,降低廢水的SS、濁度等指標(biāo),以滿足反滲透的進(jìn)膜要求;
4、膜過濾處理后的采油廢水經(jīng)過脫鹽處理,脫除水中的金屬離子,降低含鹽量。
5、通過本發(fā)明方法,實(shí)現(xiàn)對(duì)采油廢水50~65%的回收率。