高低溫?zé)煔庑L(fēng)蒸發(fā)技術(shù)處理脫硫廢水
中國污水處理工程網(wǎng) 時間:2018-4-5 8:52:55
污水處理技術(shù) | 匯聚全球環(huán)保力量,降低企業(yè)治污成本
1工藝流程簡介
該技術(shù)的工藝路線如下
1)從煙氣系統(tǒng)空預(yù)器前的高溫?zé)煔舛我∫还筛邷責(zé)煔,再從空預(yù)器后的高溫?zé)煔舛我∫还傻蜏責(zé)煔夥謩e進(jìn)入濃液蒸發(fā)器,使其作為濃液蒸發(fā)的熱源和濃液載體。
2)將脫硫廢水處理所得濃液經(jīng)泵送至濃液蒸發(fā)器,為使進(jìn)入蒸發(fā)器中的濃液能被煙氣快速蒸發(fā),濃液進(jìn)入蒸發(fā)器時被霧化為細(xì)小霧滴,采用兩相流霧化噴嘴,利用壓縮空氣進(jìn)行霧化。
3)高溫?zé)煔鈴恼舭l(fā)器頂部進(jìn)入蒸發(fā)器。
4)濃液霧化噴嘴布置在煙氣均流設(shè)施后,霧化噴嘴分多組,以方便在線清潔維護(hù)。
5)低溫?zé)煔鈴撵F化噴嘴后分幾路沿切線方向進(jìn)入蒸發(fā)器,為霧滴蒸發(fā)提供持續(xù)熱源,同時,由于切向進(jìn)風(fēng)煙氣沿筒壁速度快,使霧滴不碰壁,避免結(jié)垢。采用如此分級煙氣進(jìn)入的設(shè)計,一方面,有利于霧滴在煙氣中均布;另一方面,可減少高溫?zé)煔獾氖褂昧,?jié)約運行成本。
6)濃液蒸發(fā)后,液體中的離子將生成鹽,以固體細(xì)粉形式進(jìn)入煙氣中,然后通過煙氣均布裝置進(jìn)入除塵器入口煙道。
7)濃液蒸發(fā)后,產(chǎn)生的水蒸汽在脫硫系統(tǒng)中冷凝下來。
2技術(shù)創(chuàng)新點
(1)該技術(shù)的創(chuàng)新點在于采用高、低溫?zé)煔庾鳛闈庖赫舭l(fā)熱源,既可保證液體有效蒸發(fā),又可減少使用高溫?zé)煔饬,降低運行成本。
(2)蒸發(fā)器設(shè)計采用高溫?zé)煔鈴捻敳窟M(jìn)入,通過放大氣流截面和煙氣整流裝置后,使煙氣流速均勻,速度適當(dāng)。液體噴灑在此位置,更有利于噴灑的水霧分散。而后,有一路或多路低溫?zé)煔膺M(jìn)氣,低溫?zé)煔庋赝搀w圓周的切線方向進(jìn)入,低溫?zé)煔獾募尤,保證水分蒸發(fā)的熱源,低溫?zé)煔庋厍芯方向進(jìn)入,使蒸發(fā)器內(nèi)的煙氣流向由原來的直線流變?yōu)槁菪搅鲃,且筒壁流速較快。一方面,增長氣流路徑,有利蒸發(fā);另一方面,使霧滴不易黏在壁上,防止結(jié)垢。
(3)濃液的噴灑采用多支噴霧噴嘴,采用雙相流霧化噴嘴,雙相流霧化噴嘴可降低霧化粒徑,采用多支噴霧噴嘴,可保證蒸發(fā)器在工作時有一支噴霧噴嘴處在自清潔狀態(tài),保證蒸發(fā)器工作的穩(wěn)定性。
(4)采用先進(jìn)的CFD流場模擬技術(shù),確定適當(dāng)?shù)膰娚湮恢煤蛧娙虢嵌燃皣娙肓,保證濃縮液的霧化顆粒與煙氣充分接觸,使液滴完全蒸發(fā)。
(5)高濕度高鈉鹽成分煙氣摻入原煙氣中,降低了煙塵比電阻,提高了下游除塵器的除塵效率,有一舉兩得的效果。
3技術(shù)難點與影響因素
該技術(shù)難點在于
1)合適的高溫?zé)煔、低溫(zé)煔獗壤,高溫(zé)煔獠捎檬∶浩鞒隹、SCR反應(yīng)器入口的煙氣,低溫?zé)煔獠捎每諝忸A(yù)熱器后的煙氣作為蒸發(fā)濃液水分熱源,如果取用的熱煙氣較多,將會影響鍋爐的效率,取用熱煙氣較少,不利于濃液蒸發(fā)。
2)噴嘴布置位置的選擇,既要使霧滴均勻分散到煙氣中,又要防止霧化液滴噴射到蒸發(fā)器壁上。
3)如何防止霧化噴嘴堵塞是技術(shù)難點,廢水濃液鹽分含量高、容易結(jié)晶結(jié)垢堵塞噴嘴。
4煙氣引取位置的影響
該技術(shù)引取煙氣的位置有
1)省煤器出口,SCR反應(yīng)器入口
2)SCR反應(yīng)器出口,空預(yù)器入口
3)空預(yù)器出口,電除塵器入口。以上各點的氣體參數(shù)見表
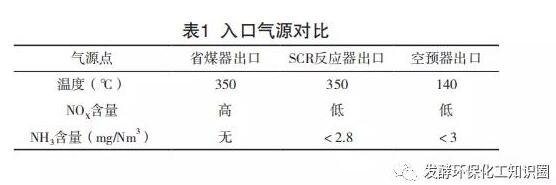
(1)選擇省煤器出口、SCR反應(yīng)器入口的煙氣作為熱源,蒸發(fā)1m3的濃縮液(含鹽量為15%,旋風(fēng)分離器出口溫度>120℃)需要熱煙氣量約10,000Nm3,現(xiàn)有300MW機組的廢水量為5~15m3,經(jīng)過預(yù)處理和膜濃縮后濃液的量為1~3m3(膜回收率按80%考慮),如按照2m3濃水進(jìn)行計算,需要熱煙氣量為2萬Nm3,300MW機組的煙氣量約為100萬Nm3,選取的煙氣量占總煙氣量的2%。因省煤器出口的NOx含量高,為300~500mg/Nm3,會使煙囪處的NOx含量上升6~10mg/Nm3。
因此該技術(shù)不選擇省煤器出口的煙氣作為熱源。
(2)選擇SCR反應(yīng)器出口、空預(yù)器入口處的NOx含量低,不會影響脫硝效果。此處煙氣溫度在310℃~420℃。以一臺300MW機組為例,假設(shè)脫硫廢水濃液為1~3m3(蒸發(fā)器出口煙溫>120℃),需要熱煙氣量1.0萬~3.0萬Nm3,300MW機組的煙氣量為100萬Nm3,抽取氣體量占總氣體量的1.0%~3.0%,對鍋爐效率有一定的影響:增加煤耗25167kg/h。如果濃液處理量為1m3,蒸發(fā)器的直徑為2m。
(3)選擇空預(yù)器出口,電除塵器入口。此處煙氣溫度為140℃~150℃,取150℃,如果以一臺300MW機組為例,假設(shè)脫硫廢水濃液為1m3(蒸發(fā)器出口煙溫>110℃),需要熱煙氣量為6萬Nm3,處理量為1m3時,旋風(fēng)分離器的尺寸直徑為5.5m。且因蒸發(fā)器有500~800Pa的壓損,因此需配置一臺風(fēng)機,使投資費用和運行費用均提高。但選取此處的煙氣作為熱源不會影響鍋爐效率。
綜上所述,通過投資成本、運行穩(wěn)定及工藝的特點綜合考慮,選擇SCR反應(yīng)器出口煙氣作為高溫?zé)嵩磳γ摿驈U水濃液進(jìn)行初步蒸發(fā),選取空預(yù)器出口煙氣作為低溫?zé)嵩磳γ摿驈U水濃液進(jìn)行再次蒸發(fā)。
霧化噴嘴的影響旋轉(zhuǎn)式霧化噴嘴
旋轉(zhuǎn)式霧化噴嘴借助了離心力和空氣動力而霧化流體,轉(zhuǎn)盤式噴嘴主要應(yīng)用于噴霧干燥設(shè)備上,國產(chǎn)離心噴霧機已有定型產(chǎn)品,如N603、N604等。噴霧干燥設(shè)備上的轉(zhuǎn)盤霧化器又有多種結(jié)構(gòu)形式,如蝶形光滑圓盤、多管圓盤(N603、N604屬于此種)、多葉圓盤、多層圓盤(也帶噴管)等。圓盤霧化器,既有液膜式霧化,也有液柱式霧化原理的霧化器,其旋轉(zhuǎn)體轉(zhuǎn)速為300020,000r/min,圓盤圓周速度為60~170m/s,可處理的料液為每小時幾升至上萬公斤,不同料液在不同霧化器上可獲得不同霧滴尺寸,數(shù)微米至數(shù)百微米。處理能力大、防堵效果好,但需盡可能提高旋轉(zhuǎn)體的轉(zhuǎn)速以保證霧化的粒徑,使得霧化范圍大,蒸發(fā)設(shè)備的直徑要求較大。
二流體霧化噴嘴
二流體霧化噴嘴利用壓縮空氣與液體的摩擦,產(chǎn)生均勻和細(xì)密的霧化效果,平均的霧化顆粒直徑在50微米以下,主要有內(nèi)混式和外混式。內(nèi)混式:氣體、液體在空氣帽和液體帽腔體內(nèi)部混合霧化,霧化原理為空氣破裂和撞擊,霧化效果理想,但不適合有一定黏性的液體。外混式:氣體、液體在噴出后,利用高速氣流對液體進(jìn)行摩擦產(chǎn)生霧化。霧化原理為摩擦和產(chǎn)生的切向應(yīng)力,霧化效果一般,尤其適合帶有一定黏性的液體。處理能力小、氣耗量大、霧化粒徑均勻,防堵效果一般。
一流體霧化噴嘴
單流體霧化噴嘴是一種在醫(yī)藥工業(yè)中廣泛應(yīng)用的霧化方式,液體由泵加壓送入噴嘴,液體在噴嘴旋轉(zhuǎn)室內(nèi)高速旋轉(zhuǎn),然后從噴嘴的小孔噴出,使液體霧化成細(xì)小的液滴。其霧化特性取決于操作壓力和噴嘴的孔徑。一般來說,細(xì)孔內(nèi)外的壓力差越高噴孔越小,霧化的液滴越細(xì),顆粒的分布越均勻;反之壓力差越小、噴孔越大,霧化的液滴越大,顆粒的分布越不均勻。處理能力及霧化效果一般,容易堵塞。不同噴嘴對比見表
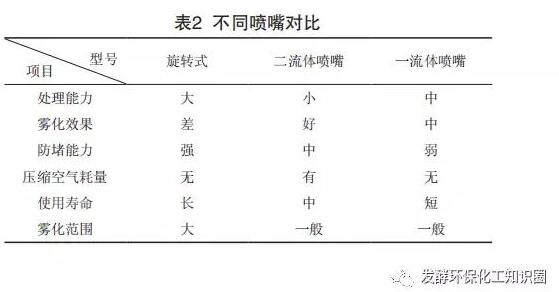
根據(jù)脫硫廢水濃液含鹽量高的特點,以及蒸發(fā)器直徑在3m左右,通過對比三種霧化噴嘴,該工程選擇處理能力小、霧化效果好、防堵能力適中、霧化形狀為細(xì)長形的二流體噴嘴(內(nèi)混式),其噴嘴霧化如圖
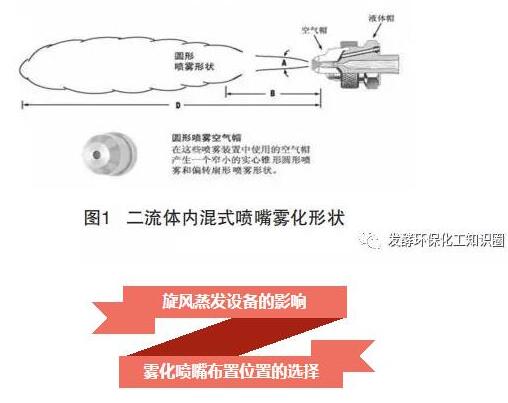
旋風(fēng)蒸發(fā)設(shè)備的影響霧化噴嘴布置位置的選擇
為保證脫硫廢水液滴充分蒸發(fā),避免未完全蒸發(fā)的液滴腐蝕蒸發(fā)器和電除塵器極板,需使煙氣在蒸發(fā)器里停留10s以上,同時使霧化噴嘴噴出來的流體盡可能地不碰壁。因此以旋風(fēng)分離器為參考模型設(shè)計蒸發(fā)器,高溫?zé)嵩磸恼舭l(fā)器頂部進(jìn)入,低溫?zé)嵩磸恼舭l(fā)器側(cè)部切線進(jìn)入,混合煙氣從蒸發(fā)器底部出去再進(jìn)入電除塵。噴嘴布置在旋風(fēng)分離器的頂部中間位置。
蒸發(fā)設(shè)備內(nèi)部件的影響
(1)擋板對蒸發(fā)設(shè)備內(nèi)部流場的影響對蒸發(fā)器器壁設(shè)置擋板(100mm)前后進(jìn)行流場模擬,圖形見圖
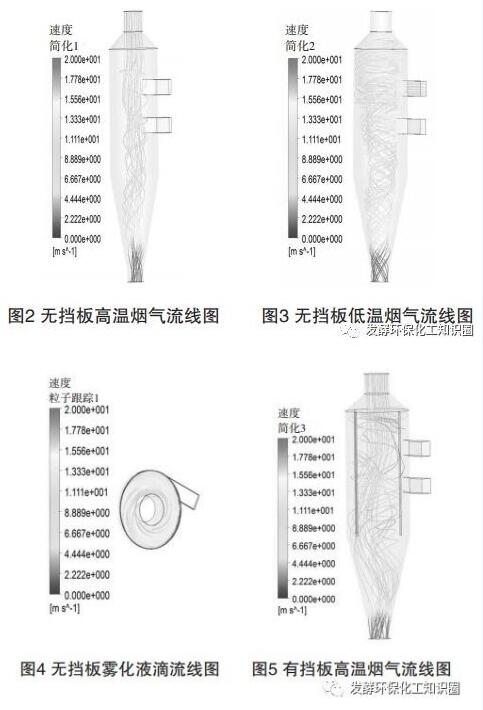
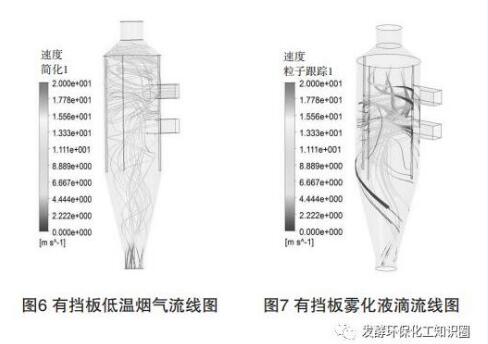
通過對比可知,蒸發(fā)器沒有設(shè)置擋板時,低溫?zé)嵩磸膫?cè)部切線進(jìn)入蒸發(fā)設(shè)備,進(jìn)入蒸發(fā)設(shè)備后,在慣性和容器壁的作用下開始進(jìn)行圓周運動,一直旋轉(zhuǎn)至蒸發(fā)設(shè)備的出口,其中越靠近容器壁的切線速度越快,在蒸發(fā)器中心切線速度基本為零,低溫?zé)嵩催M(jìn)入蒸發(fā)器后,其切向速度沒有因為流通面積的增大而大幅下降。高溫?zé)煔鈴捻敳窟M(jìn)入反應(yīng)器,高溫?zé)嵩丛谡舭l(fā)器中心切線速度基本上為零,且因低溫?zé)煔饪焖傩D(zhuǎn),在蒸發(fā)器中心產(chǎn)生一個低壓區(qū)域,因此高溫?zé)嵩春偷蜏責(zé)嵩磧烧呋旧喜换旌,高溫(zé)嵩粗苯訌恼舭l(fā)器中心區(qū)域流至蒸發(fā)器出口。因低溫?zé)嵩凑w切線速度過快,噴嘴噴出來的液滴在向心力的作用下很快就被甩至容器壁上。在蒸發(fā)器器壁設(shè)置100mm擋板時,低溫?zé)嵩磸膫?cè)部切線進(jìn)入蒸發(fā)設(shè)備,進(jìn)入蒸發(fā)設(shè)備后,在擋板的減速作用下,使切向速度下降,蒸發(fā)器中心不會產(chǎn)生明顯的低壓區(qū)域,高溫?zé)煔膺M(jìn)入蒸發(fā)器后被低溫?zé)煔鈳有D(zhuǎn),因低溫?zé)煔馇芯速度下降,噴嘴產(chǎn)生的液滴所受離心力降低,會跟著煙氣旋轉(zhuǎn)1~2圈后才會碰壁。具體聯(lián)系污水寶或參見http://www.northcarolinalenders.com更多相關(guān)技術(shù)文檔。
(2)整流板對蒸發(fā)設(shè)備內(nèi)部流場的影響為避免高溫?zé)煔庵苯訌恼舭l(fā)器中心區(qū)域流出蒸發(fā)器,在蒸發(fā)器上部椎體處設(shè)置一篩板,篩板中心開孔率為10%左右,四周開孔率為30%左右,流程模擬圖如圖8。由模擬圖8可知,高溫?zé)煔鈴捻敳窟M(jìn)入,通過放大氣流截面和煙氣整流裝置,使煙氣流速均勻,速度適當(dāng),液體噴灑在此位置,更有利于噴灑的水霧分散。
膜+高溫?zé)煔庑L(fēng)分離技術(shù)與膜+MVR蒸發(fā)制鹽技術(shù)的對比
從表3可看出,采用膜+MVR結(jié)晶蒸發(fā)技術(shù)產(chǎn)單鹽,設(shè)備初次成本高,還需要人工成本,同時設(shè)備轉(zhuǎn)動部件多,設(shè)備維修費高,6噸濃液MVR+結(jié)晶蒸發(fā)技術(shù)處理的成本比高溫?zé)煔庑L(fēng)分離處理技術(shù)的成本高很多。同時MVR+結(jié)晶蒸發(fā)技術(shù)設(shè)備容易結(jié)垢,對脫硫廢水預(yù)處理要求高,要求鈣鎂離子濃度≤50mg/L,同時得到的副產(chǎn)物NaCl純度不穩(wěn)定,工藝流程復(fù)雜。高溫?zé)煔庑L(fēng)分離處理技術(shù)工藝流程簡單,轉(zhuǎn)動設(shè)備少,無副產(chǎn)物,無需專人看守。
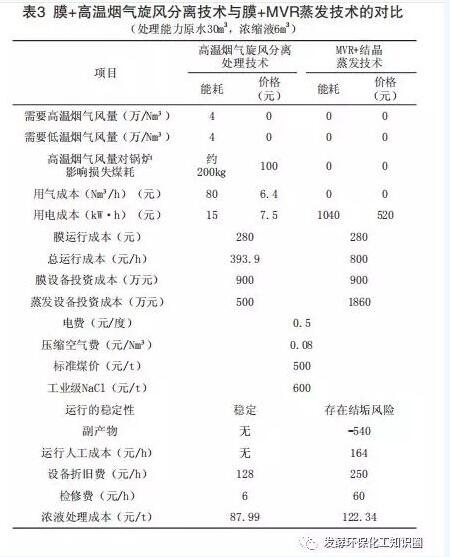
高溫?zé)煔庑L(fēng)分離處理技術(shù)充分利用了電廠鍋爐廉價的高、低溫?zé)煔庾鳛闊嵩磥碚舭l(fā)脫硫廢水濃液,利用壓縮空氣將脫硫廢水濃液霧化成100μm左右的細(xì)小液滴,采用旋風(fēng)蒸發(fā)設(shè)備,延長了煙氣在蒸發(fā)器中的停留時間,有利于脫硫廢水濃液霧化液滴充分蒸發(fā),進(jìn)而不腐蝕煙道和電除塵器極板。脫硫廢水在蒸發(fā)器里蒸發(fā)成水蒸汽進(jìn)入煙氣,水蒸汽在FGD脫硫塔里冷卻下來,可減少FGD的用水量,整個FGD工藝再無排水,可實現(xiàn)電廠脫硫廢水真正意義上的零排放。同時水蒸汽進(jìn)入煙氣,可降低煙氣的溫度和灰塵的比電阻,進(jìn)而提高電除塵的除塵效率。此外,水蒸汽進(jìn)入煙氣,提高煙氣的濕度,當(dāng)煙氣進(jìn)入FGD脫硫塔后,在噴淋層的作用下溫度下降,煙氣的水分冷凝下來,水相變的過程中可促進(jìn)PM2.5的凝并,有利于提高吸收塔對粉塵的脫除率。高溫?zé)煔庑L(fēng)分離處理技術(shù)為脫硫廢水超低排放提供一條安全、可行、工藝簡單、能耗和投資成本低的新線路。(來源:谷騰環(huán)保網(wǎng))